What Substances Make Up Iron Pot
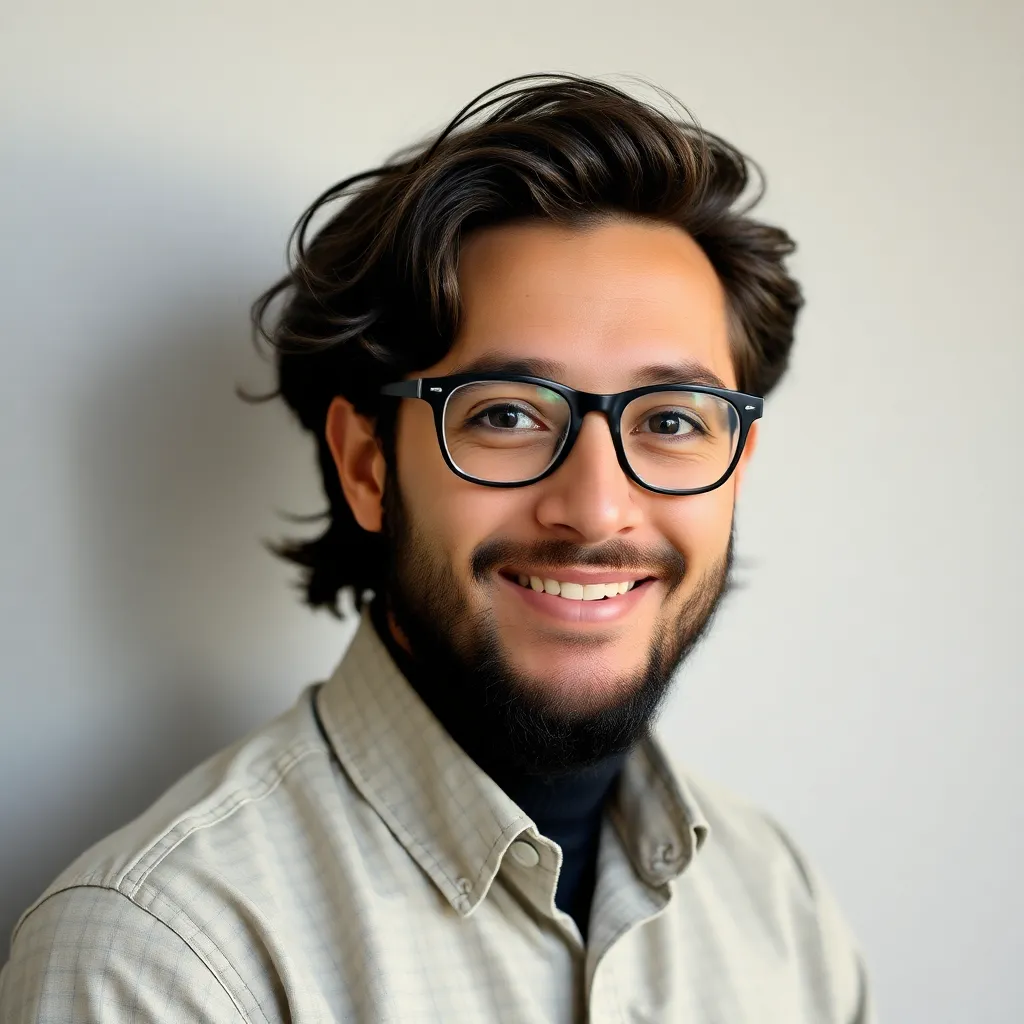
New Snow
Apr 27, 2025 · 5 min read

Table of Contents
What Substances Make Up an Iron Pot? A Deep Dive into Composition and Manufacturing
Iron pots, seemingly simple kitchen tools, possess a fascinating complexity in their composition. Understanding the substances that make up an iron pot goes beyond simple "iron"—it's a journey into metallurgy, manufacturing processes, and the subtle nuances that impact performance and longevity. This article explores the multifaceted nature of iron cookware, delving into the primary components, secondary alloying elements, manufacturing techniques, and the impact of these factors on the cooking experience.
The Foundation: Iron Itself
The primary component of an iron pot, unsurprisingly, is iron (Fe). This is the base metal that provides the pot's structure, heat conductivity, and durability. However, pure iron, while possessing excellent heat transfer properties, is relatively soft and prone to rust. This is why additional substances are crucial in the manufacturing process. The type and grade of iron used significantly influences the pot's final characteristics. For instance, cast iron and wrought iron, while both primarily iron, differ in their manufacturing processes and consequently, their properties. Cast iron, formed by pouring molten iron into a mold, possesses a denser, more brittle structure compared to wrought iron, which is forged from heated and hammered iron bars, resulting in a tougher, more malleable material.
The Role of Carbon
Crucial to understanding the properties of iron pots is the role of carbon (C). Carbon is an interstitial element—it sits within the iron's crystalline structure, influencing its hardness, strength, and brittleness. The carbon content directly impacts the type of iron produced. Steel, a crucial element in many iron pots, is an alloy of iron and carbon, typically containing between 0.02% and 2.1% carbon. Higher carbon content translates to greater hardness and strength, but also increased brittleness and reduced ductility. Therefore, manufacturers carefully control carbon content to achieve the optimal balance of strength, durability, and workability.
Alloying Elements: Enhancing Performance
Beyond iron and carbon, numerous other alloying elements are added during the manufacturing process to further refine the pot's properties. These additions address specific challenges and enhance desired characteristics.
Enhancing Strength and Durability:
- Manganese (Mn): Manganese improves the pot's strength, hardness, and wear resistance. It enhances the workability of the iron, making it easier to shape and mold during manufacturing.
- Silicon (Si): Silicon increases fluidity during the melting process, facilitating better casting and minimizing defects in cast iron pots. It also contributes to improved hardness and strength.
- Chromium (Cr): Chromium is a vital element in stainless steel, which may be used for certain parts of an iron pot, especially in higher-end models. It significantly enhances corrosion resistance, preventing rust and improving longevity.
Improving Heat Transfer and Resistance:
- Nickel (Ni): Nickel is another key component of stainless steel, improving its heat resistance and corrosion resistance, ensuring even heat distribution and easier cleaning.
- Molybdenum (Mo): Molybdenum is used in some stainless steel formulations to improve their strength and corrosion resistance at high temperatures. This is especially beneficial for pots subjected to intense heat.
- Phosphorus (P): While often present in small quantities as an impurity, phosphorus can improve the fluidity of molten iron during casting. However, excessive phosphorus can lead to embrittlement.
Other Additives and Impurities:
Many other elements can be present in trace amounts, either intentionally added or as unavoidable impurities from the raw materials. These include:
- Sulfur (S): Sulfur is generally considered an undesirable impurity because it can cause hot shortness—reduced ductility at high temperatures—making the iron brittle and difficult to work with.
- Titanium (Ti): Titanium is sometimes added to improve the grain structure and reduce the size of iron crystals, resulting in finer-grained iron with enhanced strength and toughness.
- Copper (Cu): Copper can enhance thermal conductivity but is generally not a major alloying element in iron pots.
Manufacturing Processes: Shaping the Pot
The manufacturing process significantly influences the final properties and quality of the iron pot. Different techniques lead to different microstructures and characteristics.
Cast Iron Production:
Cast iron pots are produced through a casting process. Molten iron, carefully alloyed with the desired elements, is poured into a mold (usually sand or metal). Once cooled and solidified, the cast iron pot is removed from the mold. This process allows for intricate designs and large volumes of production. However, cast iron is inherently more brittle than wrought iron.
Wrought Iron Production:
Wrought iron pots are forged from heated and hammered iron bars. This process refines the grain structure, producing a tougher and more durable material than cast iron. However, it is a more labor-intensive and less efficient method of production. Consequently, wrought iron pots are less common.
Steel Fabrication:
Some iron pots incorporate steel components, especially in higher-end models. Steel is typically produced through various processes, including basic oxygen furnace (BOF) and electric arc furnace (EAF) methods, involving careful control of the alloying elements to achieve desired properties. Steel components may be added to create features like handles or lids.
The Importance of Seasoning: Transforming the Surface
While the substances listed above define the bulk composition of an iron pot, the surface undergoes a transformation crucial for its functionality: seasoning. Seasoning involves applying a layer of oil or fat to the pot's surface and heating it to high temperatures. This process polymerizes the oil, creating a protective layer that prevents rust, improves non-stick properties, and enhances the pot's seasoning over time. This layer is not a separate substance added but a chemical alteration of the iron's surface through a reaction with the oil.
Conclusion: A Complex Composition for a Simple Tool
The apparent simplicity of an iron pot belies the sophisticated metallurgy and manufacturing processes involved in its creation. From the base iron and its critical carbon content to the carefully chosen alloying elements and the transformative process of seasoning, the composition and manufacturing of iron pots are a testament to human ingenuity. Understanding these factors allows for a deeper appreciation of the pot's durability, heat transfer capabilities, and overall performance, making it a valued tool in kitchens worldwide. The next time you use your iron pot, remember the intricate chemistry and engineering behind its creation.
Latest Posts
Latest Posts
-
George Gershwin Usually Collaborated With The Lyricist
Apr 28, 2025
-
We Decode Messages Based On And
Apr 28, 2025
-
Some Enlightenment Thinkers Were Afraid Of This
Apr 28, 2025
-
All Of The Following Are Examples Of Enumerated Powers Except
Apr 28, 2025
-
Being A Man By Paul Theroux
Apr 28, 2025
Related Post
Thank you for visiting our website which covers about What Substances Make Up Iron Pot . We hope the information provided has been useful to you. Feel free to contact us if you have any questions or need further assistance. See you next time and don't miss to bookmark.