The Wall Of A Drying Oven Is Constructed By Sandwiching
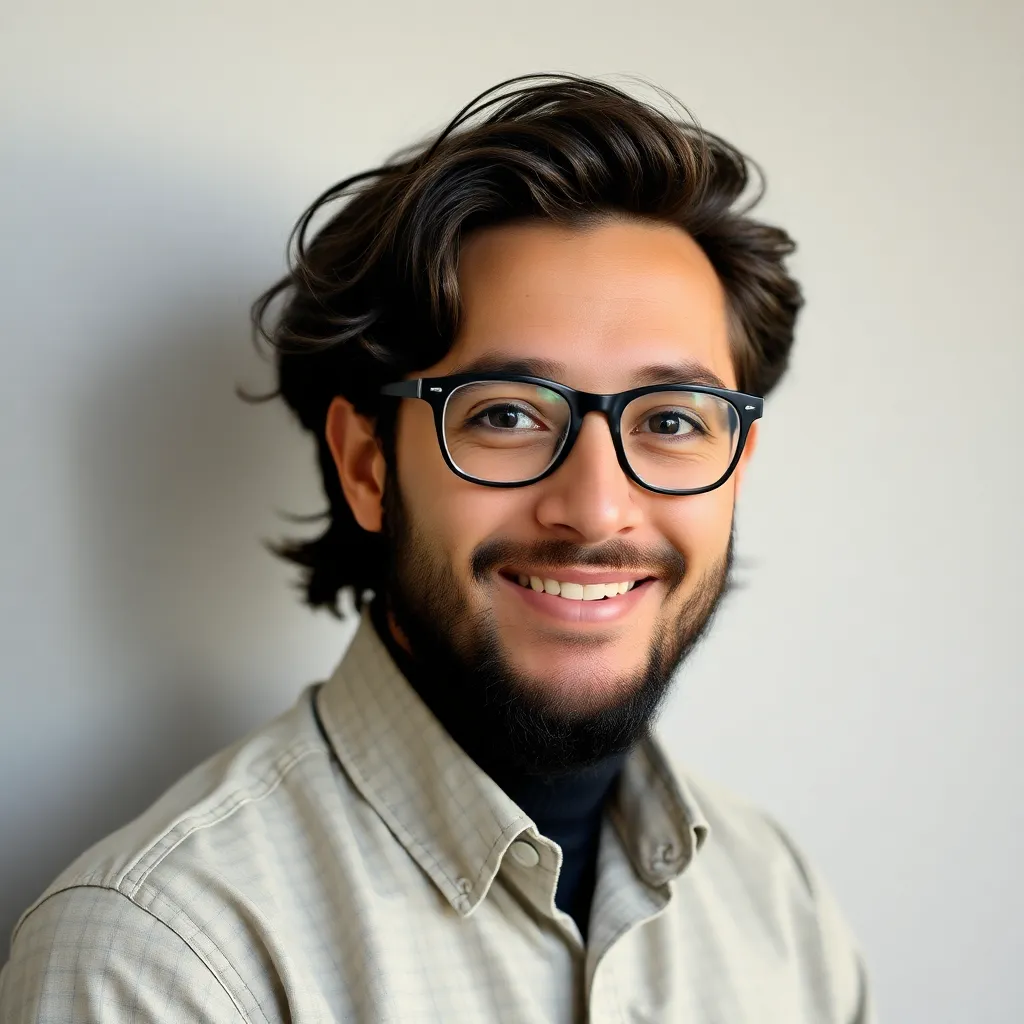
New Snow
Apr 23, 2025 · 6 min read

Table of Contents
The Wall of a Drying Oven: A Deep Dive into Sandwich Construction
The design and construction of industrial drying ovens are critical for efficient and effective operation. A key component influencing performance, longevity, and energy efficiency is the oven wall itself. Increasingly, a sandwich construction method is favored due to its superior insulation properties, cost-effectiveness, and adaptability to various oven sizes and applications. This detailed exploration delves into the nuances of sandwich construction for drying oven walls, examining the materials used, manufacturing processes, and the advantages and disadvantages of this approach.
Understanding the Sandwich Construction Principle
The "sandwich" in sandwich panel construction refers to the layering of different materials to create a composite structure. For drying oven walls, this typically involves three key layers:
1. The Outer Skins: Robust and Protective
The outer skins of the sandwich panel provide protection from the environment and contribute to the oven's overall structural integrity. Common materials include:
-
Stainless Steel: A highly popular choice due to its corrosion resistance, durability, and ease of cleaning. Stainless steel's high thermal conductivity can be mitigated through insulation choices and panel design. It’s ideal for food processing, pharmaceutical, and other hygiene-sensitive applications.
-
Galvanized Steel: A more economical option than stainless steel, offering good corrosion protection but potentially lacking the same level of hygiene suitability. Its lower cost makes it a viable alternative for less demanding applications.
-
Aluminum: Lightweight and offering good corrosion resistance, aluminum is a suitable choice, particularly where weight is a factor. However, its lower strength compared to steel may necessitate additional structural support in certain designs.
-
Composite Materials: Advanced composite materials are also gaining traction. These offer enhanced properties like improved strength-to-weight ratios and tailored thermal performance, but may come with a higher initial cost.
2. The Core: The Heart of Insulation
The core material lies between the outer skins, acting as the primary insulator. Effective insulation is paramount in drying ovens to minimize energy loss and maintain a stable temperature within the chamber. Key core materials include:
-
Polyurethane (PU): A widely used material known for its excellent thermal insulation properties, low density, and good compressive strength. PU foam is often injected or foamed in place, creating a seamless bond with the outer skins. Its versatility and relatively low cost make it a popular choice.
-
Polyisocyanurate (PIR): Offering even better insulation performance than PU foam, PIR is also more resistant to moisture absorption. However, it often comes with a slightly higher price tag.
-
Mineral Wool: A fibrous insulation material made from basalt, slag, or glass. It provides excellent thermal and acoustic insulation but can be more susceptible to moisture absorption compared to PU or PIR foams. It's often used in higher temperature applications where fire resistance is critical.
-
Phenolic Foam: A high-performance insulation material with excellent thermal and fire-resistant properties. While more costly, its superior performance often justifies the investment in demanding environments.
3. The Bond: Ensuring Structural Integrity
The bond between the outer skins and the core material is crucial for the panel's long-term performance and durability. Several methods are employed to ensure a strong and lasting bond:
-
Adhesive Bonding: High-strength adhesives are used to create a robust and uniform bond between the skins and core. This method is commonly employed for PU and PIR foams.
-
Mechanical Fastening: In certain cases, mechanical fasteners may be used in conjunction with adhesive bonding or independently to provide additional structural support. This is often more appropriate for mineral wool core materials.
-
Integrated Manufacturing Processes: Modern manufacturing techniques allow for the simultaneous formation and bonding of the core material and outer skins, resulting in a highly integrated and robust panel structure.
Manufacturing Processes for Sandwich Panels
The manufacturing process for sandwich panels significantly influences their quality and performance. Common manufacturing methods include:
-
Continuous Production Lines: High-volume production is facilitated by continuous production lines where the skins are fed through a system that simultaneously applies the core material and bonds the layers together. This allows for efficient and consistent panel production.
-
Pressing and Bonding: In this method, the core material is placed between the skins, and the entire assembly is subjected to high pressure and temperature to cure the adhesive and create a strong bond.
-
In-situ Foaming: For PU and PIR foams, in-situ foaming involves injecting the liquid foam into the space between the skins. The foam expands and fills the cavity, creating a homogenous and well-bonded sandwich panel. This allows for precise filling of complex shapes.
Advantages of Sandwich Construction for Drying Oven Walls
The popularity of sandwich construction for drying ovens stems from a range of advantages:
-
Superior Insulation: The multi-layered design effectively minimizes heat transfer, reducing energy consumption and maintaining a stable temperature within the oven. This leads to significant cost savings over the lifespan of the oven.
-
Improved Energy Efficiency: Reduced heat loss translates directly into improved energy efficiency, making sandwich panel ovens environmentally friendly and economically viable.
-
Enhanced Structural Strength: The composite nature of the sandwich panel provides a lightweight yet robust structure capable of withstanding the stresses of operation, especially important for large ovens.
-
Lightweight Design: The use of lightweight core materials reduces the overall weight of the oven, simplifying installation and reducing structural requirements.
-
Reduced Thermal Stress: The insulation provided by the core material reduces the thermal stress on the outer skins, extending the lifespan of the oven.
-
Versatile Design Options: Sandwich panels can be easily customized to fit various oven dimensions and shapes, providing flexibility in design and adaptation to specific needs.
-
Improved Safety: The use of fire-resistant core materials like phenolic foam can enhance the overall safety of the oven, minimizing the risk of fire hazards.
-
Cost-Effectiveness: While the initial cost of sandwich panels may be higher than alternative methods, the long-term savings in energy consumption often make them a more cost-effective solution.
Disadvantages of Sandwich Construction for Drying Oven Walls
Despite the many advantages, some drawbacks associated with sandwich panel construction should be considered:
-
Potential for Moisture Absorption (Certain Core Materials): Certain core materials, like mineral wool, are susceptible to moisture absorption, potentially compromising insulation performance and structural integrity. Proper sealing and moisture barriers are crucial to mitigate this risk.
-
Repair Difficulty: Damaging a sandwich panel can be challenging to repair; replacement is often the most practical solution. Careful handling and robust design are essential to prevent damage.
-
Cost of Specialized Equipment: The manufacturing process for sandwich panels may require specialized equipment, which can increase the initial investment for manufacturers.
-
Sensitivity to Temperature Extremes (Some Materials): Some core materials may exhibit reduced performance under extreme temperature fluctuations, requiring careful material selection based on operating conditions.
-
Potential for Degradation over Time: Long-term exposure to high temperatures or harsh chemicals can degrade the adhesive bond or core material, potentially compromising the panel's integrity. Careful material selection and appropriate design are critical in such situations.
Conclusion: Optimization Through Material Selection and Design
The choice of materials for the outer skins and core, as well as the bonding method, is crucial in optimizing the performance and longevity of a drying oven's sandwich panel walls. Careful consideration of the specific application, including operating temperature, humidity, and the type of materials being dried, is essential for selecting the appropriate materials and manufacturing process. By understanding the principles of sandwich construction and the properties of different materials, designers and manufacturers can create highly efficient and durable drying ovens that meet the demands of diverse industrial applications. Future research and development in advanced composite materials and manufacturing techniques hold the potential to further enhance the performance and sustainability of sandwich panel construction for drying ovens.
Latest Posts
Latest Posts
-
How Does Organizational Culture Impact The Change Process
Apr 24, 2025
-
Match Each Disorder With Its Most Effective Treatment
Apr 24, 2025
-
The Most Common Form Of Outcome Based Appraisal Is
Apr 24, 2025
-
A Monopolistically Competitive Market Has Characteristics That Are Similar To
Apr 24, 2025
-
The Two Dimensions Of Pricing Strategies Are
Apr 24, 2025
Related Post
Thank you for visiting our website which covers about The Wall Of A Drying Oven Is Constructed By Sandwiching . We hope the information provided has been useful to you. Feel free to contact us if you have any questions or need further assistance. See you next time and don't miss to bookmark.