The Proper Quantity Of Safety Stock Is Typically Determined By
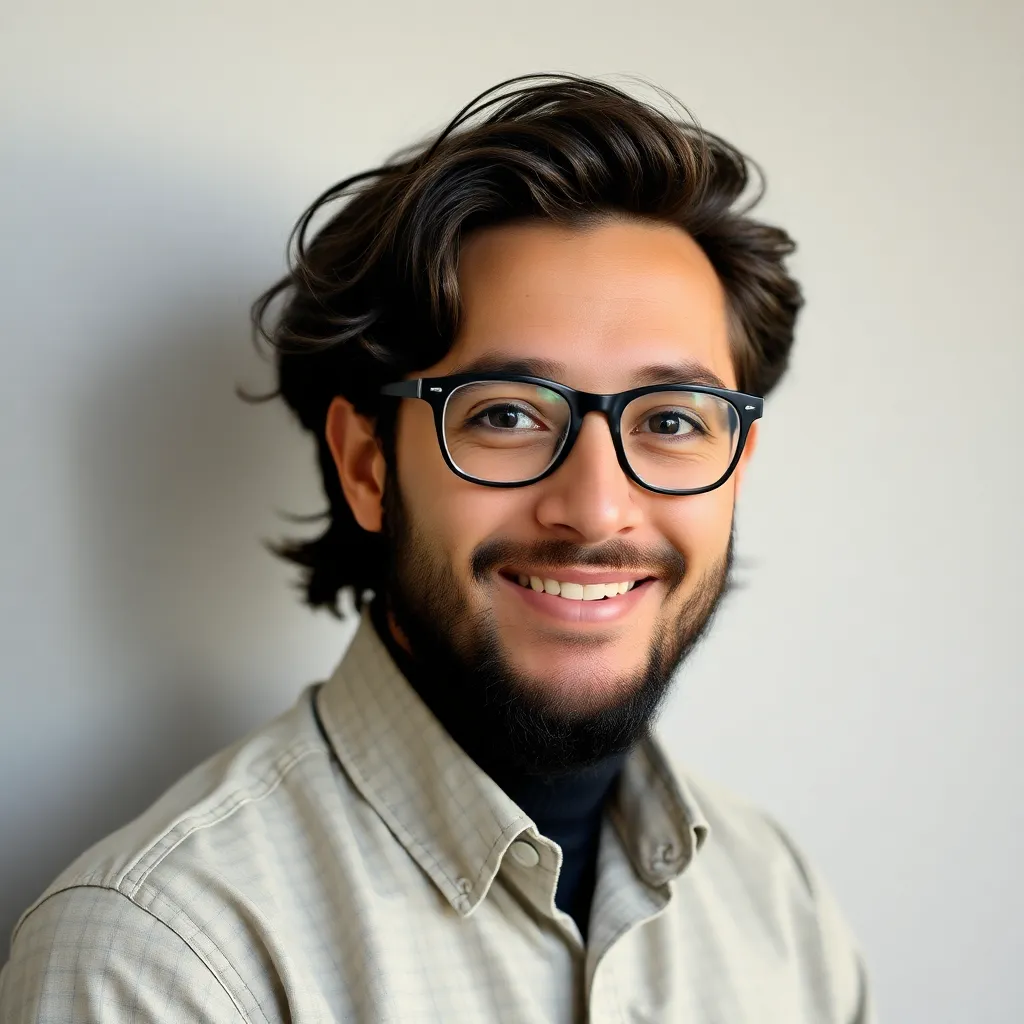
New Snow
Apr 23, 2025 · 6 min read

Table of Contents
Determining the Proper Quantity of Safety Stock: A Comprehensive Guide
Maintaining optimal inventory levels is crucial for any business. Holding too much inventory ties up capital and increases storage costs, while holding too little can lead to stockouts, lost sales, and dissatisfied customers. A key component of inventory management is safety stock – the buffer stock held to account for unexpected fluctuations in demand or lead times. Determining the proper quantity of safety stock is a delicate balancing act, and this guide will explore the various methods and factors involved.
Understanding Safety Stock: The Protective Shield of Your Inventory
Safety stock acts as a cushion against uncertainty. It protects your business from:
- Demand variability: Customer demand rarely follows a perfectly predictable pattern. Unexpected spikes in demand can quickly deplete inventory if you don't have a safety net.
- Lead time variability: The time it takes to receive an order from a supplier isn't always consistent. Delays in shipping, production issues, or supplier problems can extend lead times, leaving you vulnerable to stockouts.
- Supply chain disruptions: Unforeseen events like natural disasters, political instability, or pandemics can severely disrupt the supply chain, causing delays or complete disruptions in the flow of goods.
Key Factors Influencing Safety Stock Calculation
Several crucial factors influence the optimal level of safety stock:
1. Demand Variability: Measuring the Uncertainty
The higher the variability in demand, the more safety stock you'll need. This variability is typically measured using standard deviation. A higher standard deviation indicates greater uncertainty and a need for a larger safety stock buffer. Analyzing historical sales data is vital here. Consider:
- Seasonality: Seasonal fluctuations in demand require adjusting safety stock levels throughout the year. You'll need more safety stock during peak seasons and less during slow periods.
- Trends: Identify any upward or downward trends in demand. A growing market may require increasing safety stock to meet future demand.
- Promotional Activities: Plan for increased demand during promotional campaigns or sales events. Adding extra safety stock before these periods will prevent stockouts.
Data Analysis Tools: Statistical software packages and spreadsheet programs offer tools to calculate standard deviation and other key metrics for demand forecasting.
2. Lead Time Variability: The Time Factor
Lead time variability refers to the uncertainty in the time it takes to replenish inventory. Longer and more variable lead times necessitate higher safety stock levels. Consider:
- Supplier Reliability: Reliable suppliers with consistent lead times require less safety stock than unreliable suppliers with unpredictable lead times.
- Transportation Methods: The chosen transportation method (e.g., air freight vs. sea freight) significantly impacts lead time variability.
- Production Capacity: If your supplier has limited production capacity, lead times may be longer and more unpredictable.
Understanding Lead Time: Accurate tracking of lead times from order placement to delivery is essential for accurate safety stock calculations.
3. Service Level: Balancing Stockouts and Costs
The desired service level represents the probability of meeting demand from available inventory. A higher service level (e.g., 95% or 99%) means a lower risk of stockouts but requires higher safety stock. Conversely, a lower service level (e.g., 80%) means a higher risk of stockouts but reduces safety stock. The optimal service level depends on the cost of stockouts versus the cost of holding excess inventory.
Cost Analysis: Thoroughly analyze the costs associated with stockouts (lost sales, customer dissatisfaction) and the costs of holding excess inventory (storage, obsolescence, insurance). This analysis will guide your decision on the appropriate service level.
4. Cost of Capital: The Opportunity Cost
Holding inventory represents a significant investment. The cost of capital – the return you could have earned by investing that money elsewhere – is a crucial factor. A high cost of capital necessitates minimizing safety stock to free up capital for more profitable ventures.
Financial Analysis: Consider the current interest rates and potential investment opportunities when evaluating the cost of holding inventory.
Methods for Calculating Safety Stock
Several methods are available to calculate safety stock, each with its strengths and weaknesses:
1. Fixed-Order-Quantity (FOQ) Method: Simple and Widely Used
This method uses a fixed order quantity and a reorder point. The reorder point incorporates safety stock based on lead time demand and safety stock levels. It's relatively simple to implement but may not be optimal for products with highly variable demand or lead times.
Formula: Reorder Point = (Lead Time Demand) + (Safety Stock)
2. Reorder Point Method with Safety Stock: Accounting for Variability
This method refines the FOQ method by explicitly calculating safety stock based on demand and lead time variability. It utilizes standard deviation of demand during lead time to determine the safety stock.
Formula: Safety Stock = Z * σ<sub>LTD</sub>
Where:
- Z = Number of standard deviations corresponding to the desired service level (obtained from a Z-table).
- σ<sub>LTD</sub> = Standard deviation of lead time demand.
3. Economic Order Quantity (EOQ) Model with Safety Stock: Optimizing Ordering Costs
The EOQ model minimizes total inventory costs by balancing ordering costs and holding costs. Integrating safety stock into the EOQ model refines the order quantity and reorder point to account for demand and lead time variability. It's a more sophisticated approach than simpler methods.
Formula: EOQ = √[(2DS)/H]
Where:
- D = Annual demand
- S = Ordering cost per order
- H = Holding cost per unit per year
Safety stock is added to the reorder point calculated using the EOQ.
4. Simulation-Based Approaches: Handling Complexities
For products with highly complex demand patterns or supply chains, simulation modeling can provide more accurate safety stock recommendations. Simulation models can incorporate various factors and uncertainties to provide a comprehensive assessment of inventory risk. This approach requires specialized software and expertise.
Software: Simulation software packages allow for detailed modeling of inventory systems, considering numerous variables and uncertainties.
Implementing and Monitoring Safety Stock
Once you've determined the appropriate safety stock levels, implementing and monitoring them effectively is crucial:
- Inventory Management System: Invest in a robust inventory management system (IMS) to track inventory levels in real time, automate reorder points, and generate reports on safety stock performance.
- Regular Reviews: Regularly review safety stock levels and adjust them based on changes in demand, lead times, and other relevant factors.
- Demand Forecasting Refinement: Continuously improve demand forecasting accuracy by using more sophisticated techniques and incorporating new data.
- Supplier Relationship Management: Build strong relationships with suppliers to improve communication, reduce lead time variability, and ensure timely deliveries.
- Performance Measurement: Track key metrics such as service levels, stockout rates, and inventory turnover to evaluate the effectiveness of your safety stock strategy.
Conclusion: A Dynamic Balancing Act
Determining the proper quantity of safety stock is a crucial aspect of effective inventory management. It's a continuous process that requires careful consideration of numerous factors, including demand variability, lead time variability, service level, and cost of capital. By utilizing appropriate methods and tools, businesses can strike a balance between minimizing inventory holding costs and mitigating the risks associated with stockouts. Regular monitoring and refinement of safety stock levels will ensure optimized inventory performance and contribute to overall business success. Remember that the ideal safety stock level is not a static number but rather a dynamic variable that needs continuous adjustment to reflect the ever-changing business environment.
Latest Posts
Latest Posts
-
Classify Each Of These Simple Solutions
Apr 23, 2025
-
Which Of The Following Statements Is True Regarding Pain Management
Apr 23, 2025
-
How Do The Passages Themes Compare
Apr 23, 2025
-
Force And Motion Review Answer Key
Apr 23, 2025
-
Fix Any Errors In These Proposed Electron Configurations
Apr 23, 2025
Related Post
Thank you for visiting our website which covers about The Proper Quantity Of Safety Stock Is Typically Determined By . We hope the information provided has been useful to you. Feel free to contact us if you have any questions or need further assistance. See you next time and don't miss to bookmark.