The Philosophy Of Zero Defects Is
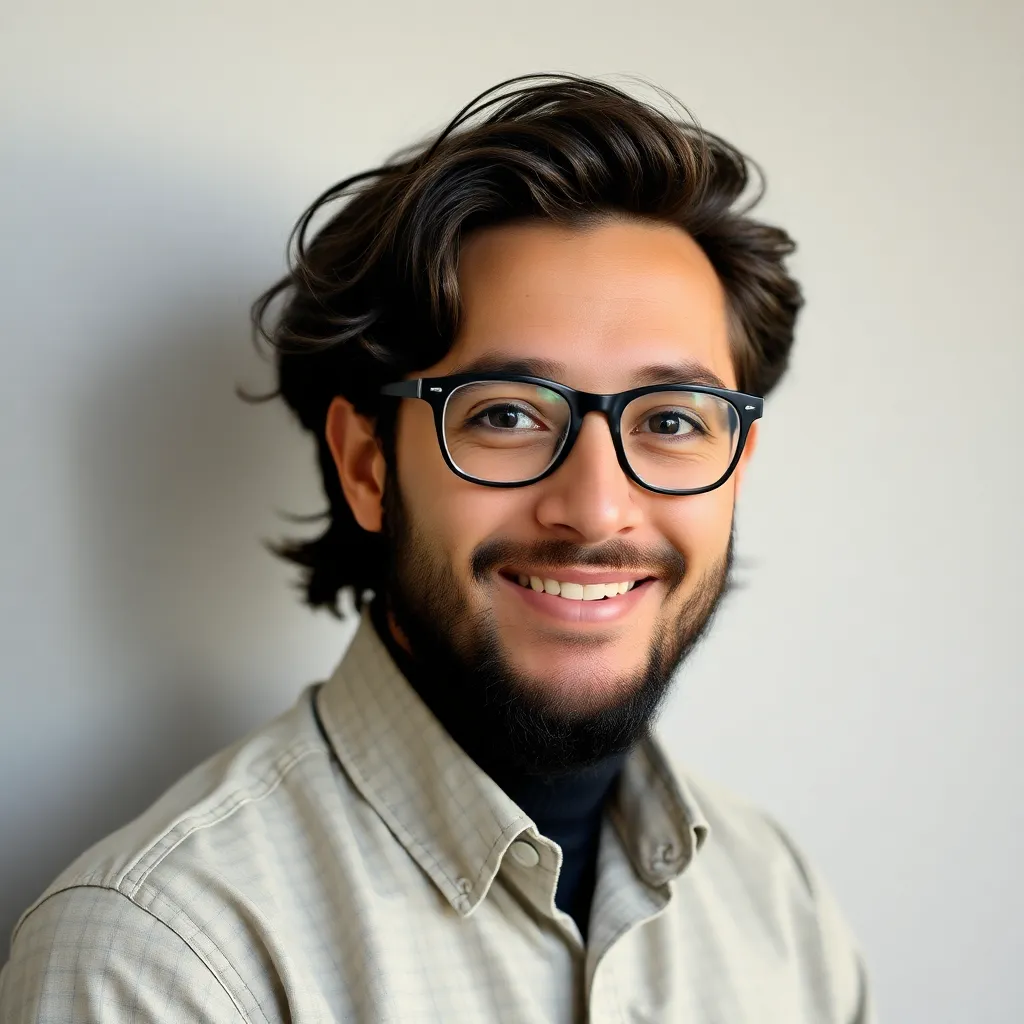
New Snow
Apr 22, 2025 · 7 min read

Table of Contents
The Philosophy of Zero Defects: Striving for Perfection in a World of Imperfection
The pursuit of perfection is a fundamental human drive. We strive for excellence in our careers, relationships, and personal endeavors. This inherent desire for flawlessness extends to the world of manufacturing and production, where the philosophy of Zero Defects (ZD) has emerged as a powerful approach to quality management. But ZD isn't merely about eliminating flaws; it's a holistic mindset that permeates every aspect of an organization, impacting everything from employee morale to profitability. This article delves deep into the philosophy of Zero Defects, exploring its core principles, practical applications, benefits, challenges, and its enduring relevance in today's competitive landscape.
Understanding the Core Principles of Zero Defects
The Zero Defects philosophy, while seemingly utopian, is grounded in a set of achievable principles. It's not about achieving absolute perfection—a statistically impossible feat—but rather about establishing a culture of continuous improvement and minimizing defects to an almost negligible level. This shift in perspective from "acceptable levels of defects" to "striving for zero" significantly alters the approach to quality control. Key principles include:
1. Prevention over Inspection:
Traditional quality control often relies heavily on end-of-line inspection, identifying defects after the product is complete. ZD flips this paradigm. It emphasizes proactive prevention through robust process design, rigorous training, and meticulous attention to detail at every stage of production. The focus shifts from finding and fixing errors to preventing them from occurring in the first place.
2. Employee Empowerment and Involvement:
ZD recognizes that quality is not solely the responsibility of a dedicated quality control department. Instead, it fosters a culture where every employee is empowered to identify and address potential quality issues. This necessitates comprehensive training, open communication channels, and a system where employees feel comfortable reporting problems without fear of retribution.
3. Continuous Improvement (Kaizen):
The pursuit of Zero Defects is an ongoing journey, not a destination. ZD embraces the philosophy of Kaizen, a Japanese term for continuous improvement. This involves regularly evaluating processes, identifying areas for improvement, and implementing changes to enhance efficiency and reduce defects. Regular feedback loops and data analysis are crucial to this iterative process.
4. Data-Driven Decision Making:
ZD relies heavily on data to identify trends, pinpoint problem areas, and measure progress. Comprehensive data collection and analysis provide insights into the root causes of defects, allowing for targeted interventions and more effective corrective actions. This data-driven approach ensures that improvements are not based on intuition but on objective evidence.
5. Customer Focus:
Ultimately, the goal of ZD is to deliver products and services that perfectly meet customer expectations. A deep understanding of customer needs and preferences is therefore paramount. Feedback mechanisms, market research, and customer relationship management (CRM) systems are essential tools for maintaining a customer-centric approach.
Implementing the Zero Defects Philosophy: Practical Strategies
Implementing ZD requires a systematic and structured approach. Several strategies can facilitate the successful adoption of this philosophy:
1. Defining Clear Quality Standards:
The first step is to establish precise and measurable quality standards. These standards should be clearly communicated to all employees and integrated into every aspect of the production process. Specific metrics should be defined to track progress and identify areas needing improvement.
2. Investing in Employee Training:
Comprehensive training is essential to equip employees with the knowledge and skills necessary to adhere to ZD principles. This includes training on quality control techniques, problem-solving methodologies, and the use of relevant tools and technologies. Regular refresher courses should be implemented to maintain consistency and address evolving needs.
3. Establishing Robust Process Controls:
Implementing robust process controls is vital to prevent defects from arising in the first place. This involves designing processes that are inherently error-proof, utilizing visual controls, implementing checklists, and establishing standardized operating procedures (SOPs).
4. Implementing Feedback Mechanisms:
Effective feedback mechanisms are crucial to identify potential quality issues early on. This could include regular quality audits, employee feedback sessions, customer surveys, and the use of suggestion boxes. All feedback should be carefully analyzed and used to drive process improvements.
5. Utilizing Technology:
Technology plays a crucial role in supporting the ZD philosophy. Automated quality control systems, data analytics tools, and sophisticated software solutions can enhance efficiency, improve accuracy, and provide valuable insights into the production process.
Benefits of Adopting a Zero Defects Approach
The benefits of embracing the ZD philosophy extend far beyond simply reducing the number of defects. These benefits include:
1. Improved Product Quality:
The most obvious benefit is a significant improvement in product quality. This translates to increased customer satisfaction, stronger brand reputation, and enhanced customer loyalty.
2. Reduced Costs:
While the initial investment in implementing ZD may seem substantial, the long-term cost savings are significant. Reducing defects minimizes waste, rework, and scrap, leading to lower production costs.
3. Enhanced Productivity:
By streamlining processes and minimizing errors, ZD can lead to increased efficiency and productivity. This allows organizations to produce more products or services with the same resources or achieve the same output with fewer resources.
4. Improved Employee Morale:
Empowering employees and recognizing their contributions to quality fosters a sense of ownership and pride. This results in improved employee morale, increased job satisfaction, and reduced employee turnover.
5. Enhanced Competitiveness:
In today's competitive marketplace, delivering high-quality products and services is crucial for success. By embracing ZD, organizations can gain a competitive edge by providing superior products and exceeding customer expectations.
Challenges in Achieving Zero Defects
While the benefits of ZD are undeniable, achieving it presents certain challenges:
1. Cultural Resistance to Change:
Implementing ZD requires a significant cultural shift within an organization. Overcoming resistance to change from employees accustomed to traditional quality control methods can be a major hurdle.
2. High Initial Investment:
The upfront investment in training, technology, and process improvements can be substantial. This can be a deterrent for some organizations, particularly smaller businesses.
3. Measurement Difficulties:
Defining and measuring "zero defects" can be challenging. Defining acceptable tolerance levels and setting realistic goals are crucial to avoid setting unrealistic expectations.
4. Maintaining Momentum:
Sustaining the momentum of continuous improvement over the long term requires consistent effort and unwavering commitment from all stakeholders. This demands a strong leadership role in championing ZD and continually reinforcing its importance.
5. Human Error:
Despite best efforts, human error remains a factor in production. While ZD aims to minimize errors, it recognizes the inherent limitations of human capabilities. Developing robust systems to mitigate human error is crucial.
Zero Defects in the Modern Context: Adapting to the Future
The ZD philosophy remains highly relevant in today's dynamic business environment. However, its successful implementation requires adaptation to the evolving technological landscape and market demands. Key considerations include:
-
Integration of advanced technologies: Leveraging technologies such as AI, machine learning, and automation can significantly enhance quality control and reduce human error. Predictive analytics can also play a critical role in identifying potential defects before they occur.
-
Focus on data analytics: Sophisticated data analytics techniques allow for deeper insights into production processes, enabling targeted improvements and more effective resource allocation. This data-driven approach is essential for continuous improvement in a ZD framework.
-
Emphasis on agile methodologies: Agile methodologies promote flexibility and responsiveness to changing market demands. Integrating agile principles into the ZD framework allows organizations to adapt quickly to evolving customer needs and technological advancements.
-
Supply chain integration: Quality should not be limited to internal processes. Extending the ZD philosophy throughout the entire supply chain ensures that quality is maintained from the sourcing of raw materials to the delivery of finished products.
-
Sustainability considerations: Integrating sustainability principles into the ZD framework is increasingly important. Reducing waste, minimizing environmental impact, and using eco-friendly materials are crucial aspects of achieving true quality in the 21st century.
Conclusion: The Enduring Power of Striving for Zero Defects
The philosophy of Zero Defects, while demanding, offers a powerful roadmap for organizations striving for excellence. It's not about achieving a mythical state of absolute perfection, but about cultivating a culture of continuous improvement, proactive prevention, and unwavering commitment to quality. By embracing ZD principles and adapting them to the modern context, organizations can achieve significant improvements in product quality, reduce costs, enhance productivity, and boost their competitive advantage in a rapidly evolving global marketplace. The journey towards zero defects is an ongoing process of learning, adapting, and striving for ever-greater levels of excellence. The ultimate reward is a stronger, more resilient, and ultimately more successful organization.
Latest Posts
Latest Posts
-
What Does Mhm Mean On Snapchat
Apr 22, 2025
-
Classify The Following Triangle Check All That Apply
Apr 22, 2025
-
Distance And Displacement Worksheet With Answer Key
Apr 22, 2025
-
The Combining Form For Fat Is
Apr 22, 2025
-
The Term Used To Describe A Disease Causing Microorganism Is
Apr 22, 2025
Related Post
Thank you for visiting our website which covers about The Philosophy Of Zero Defects Is . We hope the information provided has been useful to you. Feel free to contact us if you have any questions or need further assistance. See you next time and don't miss to bookmark.