Report Three Types Of Inventory On The Balance Sheet
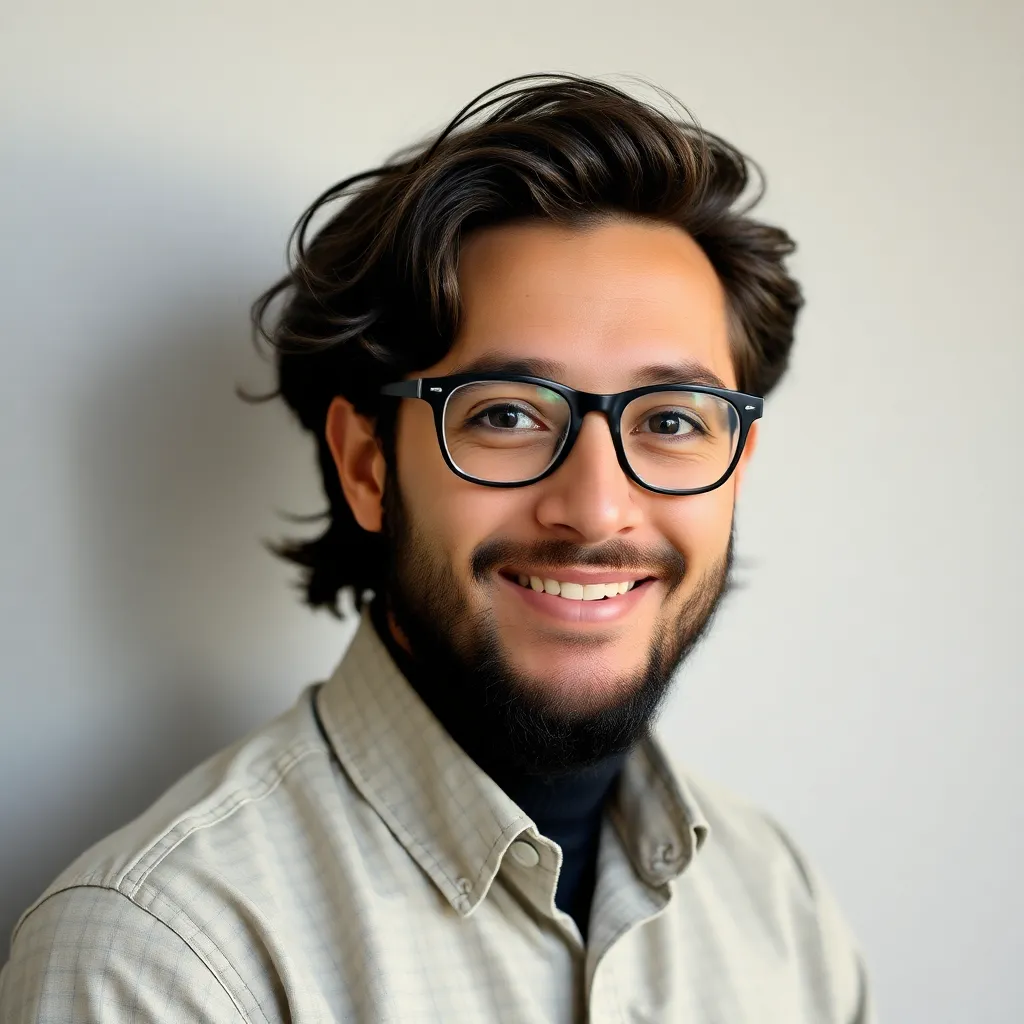
New Snow
Apr 25, 2025 · 6 min read

Table of Contents
Three Types of Inventory on the Balance Sheet: A Comprehensive Guide
Inventory is a crucial asset for many businesses, representing the raw materials, work-in-progress, and finished goods readily available for sale. Understanding the different types of inventory and how they're presented on the balance sheet is vital for accurate financial reporting and effective business management. This comprehensive guide will delve into the three primary inventory classifications – raw materials, work-in-process (WIP), and finished goods – explaining their characteristics, valuation methods, and impact on the balance sheet. We'll also explore the implications of inventory management on profitability and overall business health.
What is Inventory?
Inventory encompasses all the goods a company holds for the purpose of sale in the ordinary course of business. It represents a significant portion of a company's current assets and directly impacts its profitability. Effective inventory management is crucial for minimizing storage costs, preventing obsolescence, and ensuring sufficient stock to meet customer demand. Mismanagement can lead to stockouts, lost sales, and ultimately, reduced profits.
The Three Main Types of Inventory
Businesses categorize inventory into three main types:
1. Raw Materials: The Foundation of Production
Raw materials are the basic inputs used in the production process. These are the unprocessed materials that undergo transformation to become finished goods. Examples include:
- Manufacturing: Steel for a car manufacturer, cotton for a textile company, wood for a furniture maker.
- Retail: Individual components or parts for assembled goods.
- Food Service: Unprocessed ingredients like flour, sugar, and vegetables.
Characteristics of Raw Materials:
- Unprocessed or minimally processed: They haven't undergone significant transformation.
- Purchased from external suppliers: They are acquired from outside sources.
- Form the basis for finished goods: They are the starting point of the production process.
Valuation of Raw Materials: Raw materials are typically valued at their cost, which includes the purchase price, freight charges, and any import duties.
2. Work-in-Process (WIP): The Transformation Stage
Work-in-process (WIP) inventory represents goods that are partially completed but still undergoing production. These are items in various stages of manufacturing, awaiting further processing before becoming finished goods. Examples include:
- Manufacturing: A partially assembled car chassis, a half-finished garment, or a partially baked loaf of bread.
- Construction: A building under construction, or a partially completed road.
- Software Development: A software application in the testing phase.
Characteristics of WIP:
- Partially completed goods: They are in the midst of the production process.
- Involves multiple stages of production: They require further transformation before being ready for sale.
- Difficult to assign a precise value: Determining the value of WIP can be complex due to the incompleteness of the product.
Valuation of WIP: The valuation of WIP is more complex than raw materials. It typically includes the cost of raw materials used, direct labor costs, and a portion of manufacturing overhead allocated to the specific products. Common methods used for WIP valuation are:
- First-In, First-Out (FIFO): Assumes that the oldest units are completed and sold first.
- Last-In, First-Out (LIFO): Assumes that the newest units are completed and sold first (LIFO is less common under IFRS).
- Weighted-Average Cost: Calculates an average cost per unit based on the total cost of goods available for sale divided by the number of units.
3. Finished Goods: Ready for Sale
Finished goods are completed products ready for sale to customers. These are the end result of the production process and represent the company's sellable inventory. Examples include:
- Manufacturing: Cars, clothes, furniture, electronics.
- Retail: Packaged consumer goods, books, and clothing.
- Food Service: Prepared meals, baked goods, and ready-to-eat snacks.
Characteristics of Finished Goods:
- Completely processed and ready for sale: They have undergone all necessary manufacturing steps.
- Stored in warehouses or retail locations: They are available for immediate sale.
- Represent the company's primary revenue source: Their sale directly generates revenue.
Valuation of Finished Goods: Similar to WIP, finished goods are valued using the same methods: FIFO, LIFO, and weighted-average cost. The chosen method significantly impacts the reported cost of goods sold (COGS) and ultimately the company's net income.
Inventory on the Balance Sheet
Inventory is reported as a current asset on the balance sheet. This is because it's expected to be converted into cash within one year or the company's operating cycle, whichever is longer. The balance sheet presents the value of inventory at a specific point in time. The accuracy of this valuation is critical, as it directly affects the company's overall financial position and profitability.
Inventory Turnover Ratio: A Key Performance Indicator
The inventory turnover ratio is a vital metric that measures how efficiently a company manages its inventory. It indicates the number of times inventory is sold and replenished during a specific period. A higher turnover ratio generally suggests efficient inventory management, while a lower ratio might indicate overstocking or slow-moving inventory. The formula for inventory turnover is:
Inventory Turnover = Cost of Goods Sold / Average Inventory
Where average inventory is calculated as (Beginning Inventory + Ending Inventory) / 2.
Impact of Inventory Management on Profitability
Efficient inventory management is critical for maximizing profitability. Careful planning and control can minimize:
- Storage costs: Reducing the amount of space needed to store inventory.
- Obsolescence costs: Minimizing losses from outdated or unsaleable products.
- Carrying costs: Expenses associated with holding inventory, including insurance, taxes, and potential spoilage.
- Stockout costs: Lost sales and potential damage to customer relationships due to insufficient stock.
The Importance of Accurate Inventory Tracking
Accurate inventory tracking is the cornerstone of effective inventory management. This involves using a robust inventory management system to monitor stock levels, track movements, and identify potential issues such as slow-moving items or potential shortages. Modern inventory management systems often incorporate barcode scanning, RFID technology, and sophisticated software for real-time inventory visibility.
Choosing the Right Inventory Valuation Method
The choice of inventory valuation method (FIFO, LIFO, or weighted-average cost) significantly impacts the financial statements. FIFO generally results in a higher net income during periods of inflation, as the cost of goods sold reflects older, lower-cost inventory. LIFO, on the other hand, results in a lower net income during inflationary periods but can offer tax advantages. The weighted-average cost method provides a smoother picture of inventory costs. The selection of the method should be consistent over time and should be disclosed in the financial statements.
The Role of Technology in Inventory Management
Technology plays a crucial role in modern inventory management. Software solutions provide real-time visibility into inventory levels, enabling businesses to make informed decisions regarding purchasing, production, and sales. Automated systems can help optimize stock levels, reduce waste, and improve efficiency. Integration with other business systems, such as point-of-sale (POS) systems and enterprise resource planning (ERP) systems, enhances data accuracy and streamlines operations.
Conclusion
Understanding the three types of inventory – raw materials, work-in-process, and finished goods – is fundamental to effective business management and accurate financial reporting. The proper classification and valuation of inventory directly impact the balance sheet, income statement, and key performance indicators like the inventory turnover ratio. By implementing robust inventory management practices and leveraging technology, businesses can optimize inventory levels, minimize costs, and maximize profitability. Continuous monitoring, accurate tracking, and the selection of an appropriate inventory valuation method are crucial for success in any industry. Regular review of inventory policies and procedures ensures the ongoing health and efficiency of the business.
Latest Posts
Latest Posts
-
Human Cardiovascular Physiology Blood Pressure And Pulse Determinations
Apr 25, 2025
-
Most Employers Are Levied A Tax On Payrolls For
Apr 25, 2025
-
Maternal Newborn Online Practice 2023 B
Apr 25, 2025
-
Superposition And Reflection Of Pulses Homework Answers
Apr 25, 2025
-
A Special Processing Chip Found On Video Cards Is The
Apr 25, 2025
Related Post
Thank you for visiting our website which covers about Report Three Types Of Inventory On The Balance Sheet . We hope the information provided has been useful to you. Feel free to contact us if you have any questions or need further assistance. See you next time and don't miss to bookmark.