Labor Cost Benchmarks Are Measured By
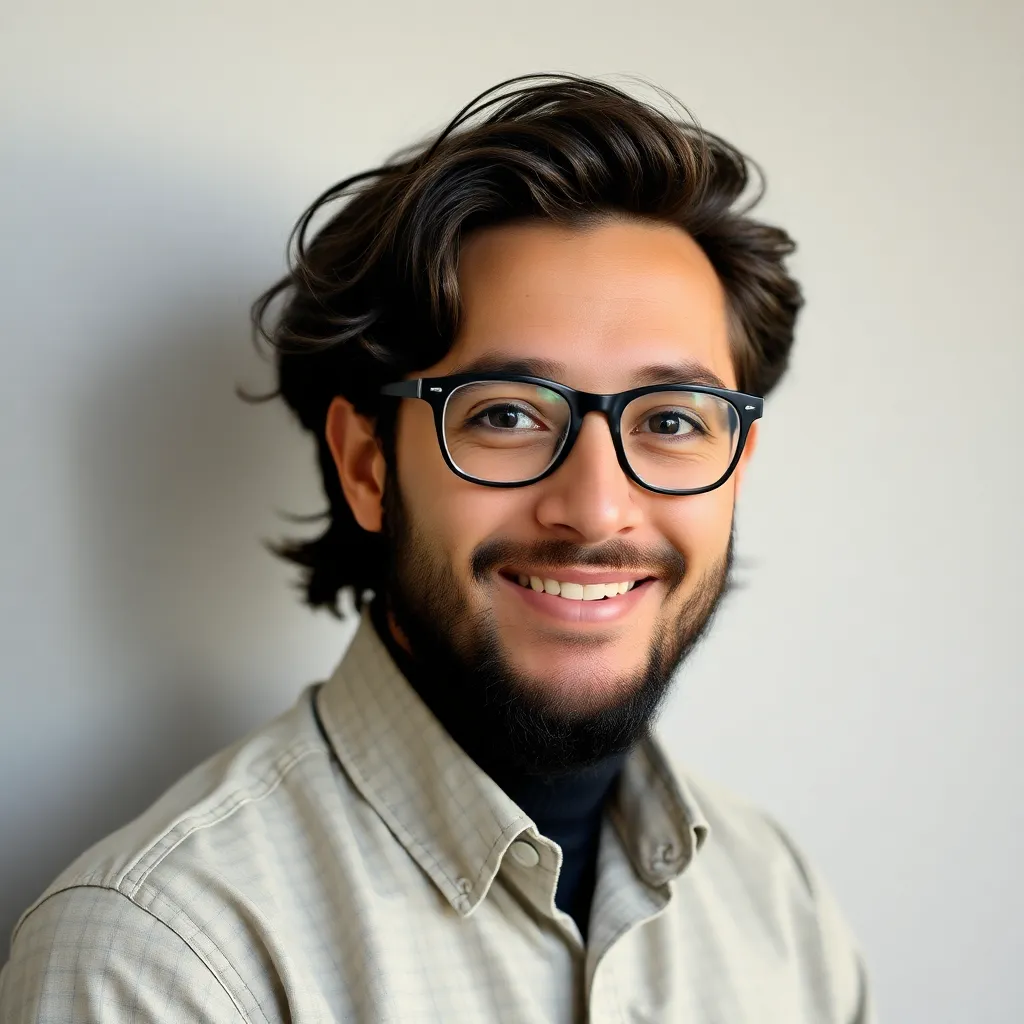
New Snow
Apr 23, 2025 · 6 min read

Table of Contents
Labor Cost Benchmarks: Measurement Methods and Key Metrics
Understanding labor costs is crucial for any business, regardless of size or industry. Effective management hinges on accurately measuring and benchmarking these costs against industry standards and internal targets. This comprehensive guide dives deep into the various methods used to measure labor cost benchmarks, exploring key metrics, influencing factors, and best practices for analysis and improvement.
Defining Labor Costs
Before delving into measurement methods, it's vital to clearly define what constitutes labor costs. These encompass all expenses directly and indirectly related to employing staff. This includes:
-
Direct Labor Costs: These are the wages, salaries, and benefits paid directly to employees involved in producing goods or services. Think of factory workers assembling products or software developers writing code.
-
Indirect Labor Costs: These support direct labor but aren't directly involved in production. Examples include salaries of supervisors, human resources personnel, maintenance staff, and administrative employees.
-
Employee Benefits: This significant component includes health insurance, retirement contributions, paid time off (sick leave, vacation), and other employee perks.
-
Payroll Taxes: Employers contribute to various payroll taxes, including Social Security, Medicare, and unemployment insurance. These add substantially to the total labor cost.
-
Training and Development Costs: Investments in employee training and professional development are considered part of labor costs.
-
Overtime Pay: Compensation for employees working beyond their regular hours adds to the overall labor cost.
Key Metrics for Measuring Labor Cost Benchmarks
Several key metrics provide valuable insights into labor costs. Understanding these metrics is essential for effective benchmarking:
1. Labor Cost as a Percentage of Revenue (LCOR):
This is a fundamental benchmark, revealing the proportion of revenue consumed by labor costs. It's calculated as:
(Total Labor Costs / Total Revenue) * 100%
A high LCOR might signal inefficiency, while a low LCOR could indicate understaffing or potential for increased profitability through strategic hiring. The ideal LCOR varies significantly across industries and business models. Benchmarking against competitors and industry averages is crucial for meaningful interpretation.
2. Labor Cost per Unit:
This metric is particularly relevant for manufacturing and production-focused businesses. It shows the labor cost associated with producing a single unit of output. It's calculated as:
Total Labor Costs / Total Units Produced
Analyzing trends in labor cost per unit helps identify areas for cost reduction, such as process improvements or technological advancements. A decreasing labor cost per unit generally indicates increased efficiency.
3. Labor Productivity:
This metric evaluates the efficiency of labor in generating output. It's often expressed as output per labor hour or output per employee. For example:
-
Output per labor hour: Total output / Total labor hours worked
-
Output per employee: Total output / Number of employees
Improving labor productivity is a key goal for cost reduction. This can be achieved through better training, process optimization, improved technology, and efficient workforce management.
4. Employee Turnover Rate:
While not directly a labor cost metric, employee turnover significantly impacts labor costs. High turnover leads to recruitment, training, and onboarding expenses, disrupting productivity. The turnover rate is calculated as:
(Number of employees who left / Average number of employees) * 100%
Reducing turnover through better employee engagement, fair compensation, and opportunities for growth is crucial for controlling labor costs.
5. Average Hourly Rate:
This metric reveals the average cost of employing an individual on an hourly basis. It's calculated as:
Total Labor Costs / Total Labor Hours
Analyzing this metric can help identify discrepancies in compensation across different departments or roles, and it can help in assessing the competitiveness of your salary structure.
Methods for Measuring and Benchmarking Labor Costs
Several methods facilitate the measurement and benchmarking of labor costs:
1. Internal Benchmarking:
Comparing labor costs across different departments, teams, or locations within the same organization. This helps identify best practices and areas for improvement. For example, comparing the LCOR of a high-performing sales team with that of a lower-performing team can reveal valuable insights.
2. External Benchmarking (Competitive Benchmarking):
Comparing labor costs against competitors in the same industry. This requires accessing industry reports, surveys, or publicly available financial data. This can be challenging, as competitors are unlikely to share detailed information. Industry associations and market research firms can be valuable resources.
3. Industry Benchmarking:
Comparing labor costs against industry averages. This provides a broader perspective on industry standards and reveals whether a company's labor costs are in line with common practices. Industry reports, government statistics, and specialized databases often provide such data.
4. Best-in-Class Benchmarking:
Comparing labor costs against the top-performing companies in the industry, regardless of size or market share. This helps identify best practices and areas for improvement in areas such as labor productivity and efficiency. Identifying these companies requires extensive research and analysis of publicly available information.
Factors Influencing Labor Costs
Several factors can significantly influence labor costs:
-
Industry: Some industries are inherently labor-intensive (e.g., healthcare, manufacturing) and will have higher labor costs than others (e.g., technology, finance).
-
Location: Labor costs vary widely based on geographical location. Areas with high costs of living tend to have higher wages and benefits.
-
Company Size: Larger companies often have more complex organizational structures and more indirect labor costs than smaller businesses.
-
Employee Skills and Experience: Highly skilled and experienced employees command higher wages.
-
Unionization: Unionized workplaces often have higher labor costs due to collective bargaining agreements.
-
Technology Adoption: Investment in automation and technology can impact labor costs both positively (reducing need for manual labor) and negatively (initial investment costs).
-
Economic Conditions: Economic downturns can reduce labor costs, while economic booms can increase them.
Analyzing and Interpreting Labor Cost Data
Analyzing and interpreting labor cost data involves several steps:
-
Data Collection: Gather comprehensive data on all aspects of labor costs, ensuring accuracy and completeness.
-
Data Cleaning: Clean the data to remove any errors or inconsistencies.
-
Metric Calculation: Calculate the key metrics discussed earlier.
-
Benchmarking: Compare the calculated metrics against internal, external, and industry benchmarks.
-
Trend Analysis: Analyze trends in labor costs over time to identify patterns and potential issues.
-
Root Cause Analysis: Investigate the root causes of any significant variances from benchmarks or trends.
-
Actionable Insights: Develop actionable insights and strategies for improving labor cost efficiency.
Best Practices for Labor Cost Management
Effective labor cost management requires a proactive and strategic approach:
-
Regular Monitoring: Continuously monitor labor costs and key metrics to identify potential problems early.
-
Strategic Workforce Planning: Develop a comprehensive workforce plan that anticipates future needs and aligns staffing levels with business objectives.
-
Effective Recruitment and Onboarding: Streamline recruitment processes and provide effective onboarding to reduce employee turnover.
-
Invest in Training and Development: Invest in employee training and development to enhance productivity and improve employee retention.
-
Process Optimization: Continuously review and optimize business processes to improve efficiency and reduce labor costs.
-
Technology Implementation: Explore opportunities to leverage technology to automate tasks, streamline workflows, and improve productivity.
-
Compensation and Benefits Review: Regularly review compensation and benefits packages to ensure competitiveness and fairness while controlling costs.
-
Performance Management: Implement robust performance management systems to ensure employees are productive and meet expectations.
Conclusion
Labor cost benchmarking is a critical process for achieving operational efficiency and profitability. By utilizing the metrics, methods, and best practices discussed in this guide, businesses can gain valuable insights into their labor costs, identify areas for improvement, and develop strategies for controlling and optimizing expenses. Remember that effective labor cost management is not about minimizing costs at the expense of employee morale and productivity, but about finding the optimal balance between cost control and workforce effectiveness. Continuous monitoring, analysis, and adaptation are crucial for achieving long-term success.
Latest Posts
Latest Posts
-
Hardware Lab Simulation 4 1 Troubleshooting Memory
Apr 23, 2025
-
Classify Each Of These Simple Solutions
Apr 23, 2025
-
Which Of The Following Statements Is True Regarding Pain Management
Apr 23, 2025
-
How Do The Passages Themes Compare
Apr 23, 2025
-
Force And Motion Review Answer Key
Apr 23, 2025
Related Post
Thank you for visiting our website which covers about Labor Cost Benchmarks Are Measured By . We hope the information provided has been useful to you. Feel free to contact us if you have any questions or need further assistance. See you next time and don't miss to bookmark.