Industries That Convert Raw Materials Into Homogeneous Products Typically Use
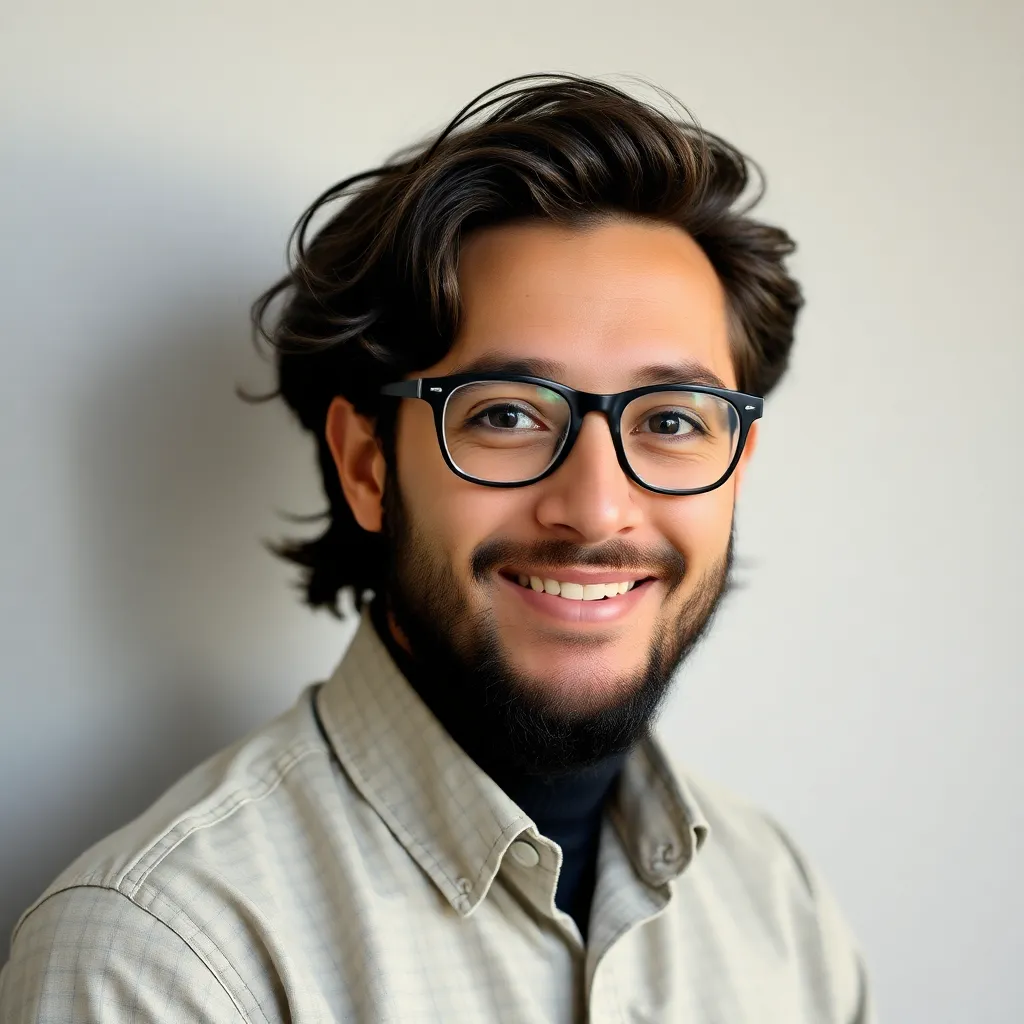
New Snow
Apr 27, 2025 · 6 min read

Table of Contents
Industries That Convert Raw Materials into Homogeneous Products: A Deep Dive
Many industries thrive on transforming raw materials into homogenous products—identical or nearly identical items produced in large quantities. This process, often involving complex manufacturing and refining procedures, underpins a significant portion of the global economy. Understanding the techniques and technologies employed by these industries is crucial for comprehending supply chains, economic trends, and the evolution of manufacturing itself. This article will explore several key industries that excel in this conversion process, analyzing their methods, challenges, and future prospects.
1. The Steel Industry: A Giant in Homogeneous Production
The steel industry stands as a prime example of large-scale homogenous product creation. From iron ore, coal, and limestone, steel mills produce vast quantities of standardized steel products. This includes:
Steel Production Processes:
- Ironmaking: Iron ore undergoes a reduction process in blast furnaces, yielding pig iron. This initial stage demands precise control over temperature and chemical composition to ensure consistent quality.
- Steelmaking: Pig iron is then refined in basic oxygen furnaces (BOFs) or electric arc furnaces (EAFs), removing impurities and adjusting the chemical composition to meet specific steel grades. The consistency in this stage is paramount for the final product's properties.
- Casting and Rolling: Molten steel is cast into various shapes (ingots, slabs, blooms) and subsequently rolled into sheets, bars, coils, and other forms. Precision in rolling mills ensures dimensional accuracy and uniformity.
Standardization and Quality Control:
Rigorous quality control measures are vital throughout the steelmaking process. Continuous monitoring of chemical composition, temperature, and physical properties ensures the steel meets exacting specifications. The industry relies heavily on standardized grades of steel (e.g., ASTM standards), enabling easy interchangeability and predictable performance across various applications.
2. The Chemical Industry: Transforming Raw Materials into Essential Products
The chemical industry encompasses a wide range of processes that convert raw materials into homogenous products. These processes often involve complex chemical reactions and sophisticated separation techniques.
Petrochemicals:
The petrochemical industry, a major subsector, transforms crude oil and natural gas into a vast array of basic chemicals, including ethylene, propylene, and benzene. These basic building blocks are then used to manufacture plastics, synthetic fibers, and countless other products. The consistency of the output is crucial for downstream processing and the reliability of final products.
Fertilizers:
The production of fertilizers heavily relies on the conversion of raw materials like natural gas, phosphate rock, and potassium salts into homogenous products. The precise control of nutrient ratios (nitrogen, phosphorus, potassium) is essential for agricultural effectiveness.
Specialty Chemicals:
The specialty chemicals sector also produces various homogenous products, such as pigments, solvents, and adhesives, often tailored to meet specific performance characteristics in downstream applications. Strict quality control is vital to ensure consistent performance and avoid any deviation from the specified properties.
3. The Cement Industry: Building the Foundation of Infrastructure
The cement industry exemplifies the conversion of raw materials into a homogenous product on a massive scale. Cement, a key component of concrete, is produced by heating a mixture of limestone, clay, and other materials in a rotary kiln at extremely high temperatures.
Cement Production Processes:
- Raw Material Preparation: Precise blending of limestone, clay, and other materials is crucial to achieving the desired chemical composition. This involves careful grinding and mixing to ensure uniformity.
- Clinker Burning: The blended raw materials are fed into a rotary kiln where they are heated to around 1450°C, forming clinker—a hard, nodular material. Temperature control and residence time in the kiln are critical for consistency.
- Cement Grinding: The clinker is then ground into a fine powder, often with the addition of gypsum to regulate setting time. The final product must meet precise particle size specifications for optimal performance.
Quality Control and Standardization:
Stringent quality control ensures that cement meets established standards for compressive strength, setting time, and other crucial properties. Standardized cement grades provide predictability and reliability in construction projects worldwide.
4. The Plastics Industry: Shaping Modern Life
The plastics industry heavily relies on the conversion of raw materials into homogenous polymers. These polymers, derived from petrochemicals, are then processed into various forms, including films, sheets, fibers, and molded parts.
Polymerization:
The heart of plastics production lies in polymerization—the chemical reaction that joins small monomer molecules into long-chain polymers. Precise control over reaction conditions ensures the desired molecular weight and properties of the polymer.
Extrusion, Injection Molding, and Other Processes:
Homogenous polymers are then processed using various techniques such as extrusion, injection molding, blow molding, and thermoforming to create standardized plastic products. The consistency of the polymer is crucial for these processes to produce items with uniform properties.
Additives and Blends:
The incorporation of additives (e.g., plasticizers, stabilizers, fillers) and blending of different polymers is common practice to tailor the properties of plastic products for specific applications. This demands careful control to maintain consistency across batches.
5. The Food Processing Industry: Transforming Raw Ingredients into Standardized Products
While often more complex due to the inherent variability of raw agricultural products, sections of the food processing industry also produce homogenous products. Examples include:
Refined Sugar:
Sugarcane or sugar beets are processed to extract sucrose and then refined into homogenous granulated sugar. The refining process removes impurities and ensures consistent crystal size and sweetness.
Vegetable Oils:
Oilseeds (soybeans, sunflowers, etc.) are processed to extract vegetable oils. Refining steps ensure consistent quality and properties, including fatty acid composition and clarity.
Processed Meats:
The production of processed meats like sausages and hot dogs involves combining various ingredients (meat, spices, additives) to achieve a consistent product. Mixing and processing techniques are key to achieving uniformity in texture, flavor, and appearance.
Challenges and Future Trends
These industries face numerous challenges, including:
- Raw Material Price Volatility: Fluctuations in the prices of raw materials significantly impact production costs and profitability.
- Sustainability Concerns: Growing environmental concerns necessitate the development of more sustainable production processes and the use of recycled materials.
- Automation and Digitalization: Automation and data analytics are transforming manufacturing processes, enhancing efficiency and quality control.
- Global Competition: Intense global competition requires continuous innovation and cost optimization to maintain market share.
The future of these industries will likely be shaped by:
- Circular Economy Principles: Increased focus on recycling and reusing materials to minimize waste and reduce environmental impact.
- Advanced Materials: The development and adoption of new materials with enhanced properties.
- Additive Manufacturing: 3D printing technologies are gaining traction, offering new possibilities for customized and on-demand production.
- Industry 4.0 Technologies: The integration of digital technologies (IoT, AI, big data) will further enhance efficiency, productivity, and quality control.
In conclusion, the industries that convert raw materials into homogenous products play a vital role in the global economy. Understanding the processes, challenges, and future trends within these sectors is crucial for anyone interested in manufacturing, supply chains, or the broader economic landscape. The ongoing evolution of these industries will be driven by innovation, sustainability concerns, and the increasing integration of digital technologies.
Latest Posts
Latest Posts
Related Post
Thank you for visiting our website which covers about Industries That Convert Raw Materials Into Homogeneous Products Typically Use . We hope the information provided has been useful to you. Feel free to contact us if you have any questions or need further assistance. See you next time and don't miss to bookmark.