Aggregate Planning Is Capacity Planning For
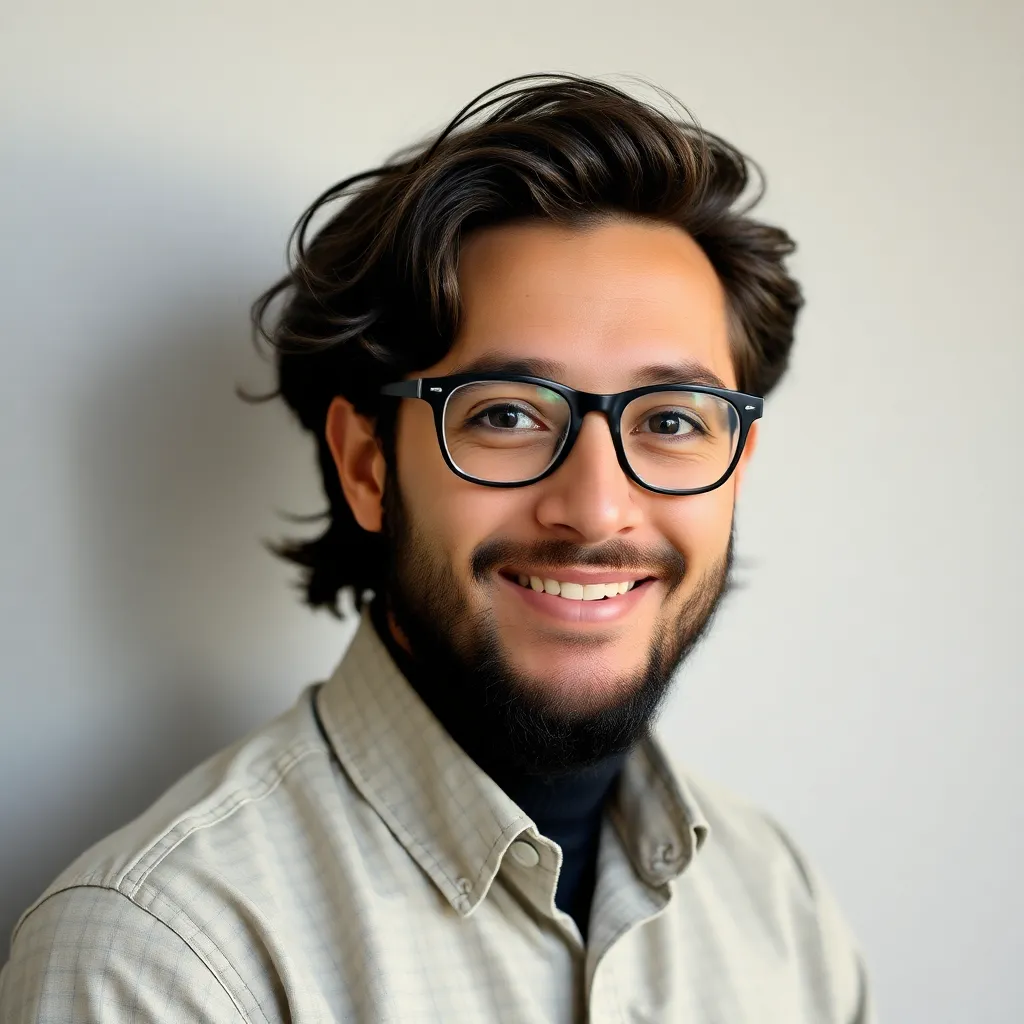
New Snow
Apr 22, 2025 · 7 min read

Table of Contents
Aggregate Planning is Capacity Planning for the Entire Organization
Aggregate planning is a crucial process in operations management that bridges the gap between long-term strategic planning and short-term operational scheduling. It's essentially capacity planning for the entire organization, focusing on aligning resources with anticipated demand over a medium-term horizon (typically 3 to 18 months). This involves making key decisions regarding production levels, workforce size, inventory levels, and subcontracting to ensure the organization can meet customer demand while minimizing costs. Understanding aggregate planning is vital for businesses of all sizes, as it directly impacts profitability, efficiency, and customer satisfaction.
Understanding the Scope of Aggregate Planning
Unlike detailed scheduling, which focuses on specific products and tasks, aggregate planning takes a broader perspective. It considers the organization's overall capacity to produce a family of products or services, rather than individual items. This aggregation simplifies the planning process, making it more manageable and less prone to errors arising from excessive detail. This high-level approach allows managers to focus on the bigger picture, identifying potential bottlenecks and imbalances before they escalate into significant problems.
Key Decisions Addressed by Aggregate Planning:
- Production Levels: Determining the optimal level of production for each product family over the planning horizon. This involves forecasting demand and considering capacity constraints.
- Workforce Levels: Adjusting the size of the workforce to match production needs. This might involve hiring, layoffs, overtime, or using temporary workers.
- Inventory Levels: Managing inventory levels to meet demand while minimizing storage costs and preventing obsolescence. This includes raw materials, work-in-progress, and finished goods.
- Subcontracting: Utilizing external resources to supplement internal production capacity during periods of high demand.
- Backlogging: Accepting orders that cannot be immediately fulfilled, potentially leading to longer lead times.
The Importance of Accurate Demand Forecasting
Accurate demand forecasting is the cornerstone of effective aggregate planning. Without a reliable forecast, any planning efforts will be severely hampered. A variety of forecasting techniques can be employed, ranging from simple moving averages and exponential smoothing to more sophisticated methods like ARIMA modeling and causal forecasting. The choice of technique depends on factors such as data availability, forecasting horizon, and the complexity of demand patterns.
Techniques for Demand Forecasting:
- Moving Averages: Calculates the average demand over a specific period, smoothing out random fluctuations.
- Exponential Smoothing: Assigns exponentially decreasing weights to older data, giving more importance to recent demand.
- ARIMA Modeling: Uses statistical techniques to identify patterns and trends in historical demand data.
- Causal Forecasting: Uses regression analysis to identify relationships between demand and other variables, such as economic indicators or marketing campaigns.
The accuracy of the forecast significantly impacts the effectiveness of the entire planning process. Therefore, it's essential to regularly review and refine the forecasting methods, incorporating new data and adjusting for unforeseen events. Continuous monitoring and adjustments are crucial to maintain the relevance of the plan.
Capacity Planning: Matching Resources with Demand
Aggregate planning directly addresses capacity planning by aligning available resources with forecasted demand. This involves evaluating various capacity options, including:
Capacity Options:
- Level Production Strategy: Maintaining a constant production rate throughout the planning horizon, relying on inventory to absorb demand fluctuations. This minimizes workforce disruptions but can lead to higher inventory costs.
- Chase Demand Strategy: Adjusting production levels to match demand fluctuations. This minimizes inventory costs but can lead to higher workforce costs due to hiring and layoffs.
- Mixed Strategy: Combining elements of both level production and chase demand, attempting to balance the trade-offs between inventory and workforce costs. This often involves a more nuanced approach, considering specific constraints and priorities.
The selection of the appropriate capacity strategy depends on several factors, including:
- Product characteristics: Perishable goods may require a chase demand strategy, while durable goods might benefit from a level production strategy.
- Production processes: Flexible manufacturing systems allow for greater responsiveness to demand changes, facilitating a chase demand strategy.
- Workforce considerations: The availability of a flexible workforce might make a chase demand strategy more feasible.
- Inventory costs: High inventory holding costs may favor a chase demand strategy, while low costs might support a level production strategy.
- Backorder costs: The cost of delaying customer orders influences the choice between meeting demand immediately or accepting backorders.
Optimizing Aggregate Plans: Cost Considerations and Constraints
Optimizing aggregate plans involves finding the best balance between satisfying customer demand and minimizing costs. This necessitates a thorough understanding of all relevant costs, including:
Relevant Costs:
- Production Costs: Costs associated with manufacturing goods or providing services, including materials, labor, and overhead.
- Inventory Holding Costs: Costs associated with storing inventory, including warehousing, insurance, and obsolescence.
- Hiring and Layoff Costs: Costs associated with recruiting, training, and separating employees.
- Overtime Costs: Costs associated with paying employees for working beyond their regular hours.
- Subcontracting Costs: Costs associated with outsourcing production to external suppliers.
- Backorder Costs: Costs associated with delaying customer orders, including lost sales and customer dissatisfaction.
Aggregate planning models often incorporate these cost elements to evaluate the financial implications of different planning strategies. Linear programming and simulation techniques are frequently employed to find optimal solutions that minimize overall costs while satisfying demand constraints.
Integrating Aggregate Planning with Other Business Functions
Effective aggregate planning requires close coordination with other business functions, including:
Integration with Other Functions:
- Marketing and Sales: Close collaboration ensures that demand forecasts are accurate and reflect market realities.
- Finance: Financial constraints and investment opportunities influence the feasibility of different planning strategies.
- Human Resources: Ensuring sufficient workforce availability and managing employee relations are crucial for implementing the chosen strategy.
- Supply Chain Management: Managing the flow of materials and coordinating with suppliers are essential for successful execution.
This integrated approach ensures that the aggregate plan aligns with the overall business objectives and is effectively implemented across the organization.
Advanced Aggregate Planning Techniques
While basic aggregate planning models can be effective, more sophisticated techniques can provide greater accuracy and optimization. These include:
Advanced Techniques:
- Linear Programming: A mathematical optimization technique that can be used to find the optimal production plan that minimizes costs while satisfying demand and capacity constraints.
- Simulation: A technique that uses computer models to simulate the effects of different planning strategies under various scenarios. This allows for risk assessment and the identification of potential problems before they occur.
- Management Science Software: Specialized software packages are available that can facilitate the aggregate planning process, providing sophisticated modeling, optimization, and reporting capabilities.
These advanced techniques can be particularly valuable in complex situations with multiple products, uncertain demand, and multiple capacity constraints.
Monitoring and Control: Adapting to Change
Once an aggregate plan is implemented, it's crucial to monitor its performance and make adjustments as needed. This requires regular tracking of key performance indicators (KPIs), including production levels, inventory levels, workforce utilization, and customer satisfaction.
Monitoring and Control:
- Performance Measurement: Regular review of key performance indicators (KPIs) to identify deviations from the plan.
- Variance Analysis: Investigating the causes of deviations from the plan and taking corrective actions.
- Plan Adjustments: Modifying the aggregate plan based on changes in demand, capacity, or other factors.
The ability to adapt to changing circumstances is vital for maintaining the effectiveness of the aggregate plan and ensuring the organization's ability to meet customer demand consistently.
Conclusion: The Strategic Value of Aggregate Planning
Aggregate planning is far more than simply a tactical exercise; it's a crucial strategic tool for aligning resources with anticipated demand. By taking a holistic view of the organization's capacity and incorporating relevant costs and constraints, aggregate planning allows businesses to optimize their operations, improve profitability, and enhance customer satisfaction. The consistent application of robust forecasting, appropriate capacity strategies, and ongoing monitoring ensures that the organization is well-positioned to meet the challenges of a dynamic business environment. Investing in advanced planning techniques and ensuring seamless integration with other business functions further amplifies the strategic value of aggregate planning, contributing significantly to the long-term success of the organization.
Latest Posts
Latest Posts
-
Compare Types Of Investment Funds Answer Key
Apr 22, 2025
-
Advanced Pathophysiology For Nurse Practitioners Test Bank Pdf
Apr 22, 2025
-
Piggy In Lord Of The Flies Quotes
Apr 22, 2025
-
Unit 3 Parent Functions And Transformations Answers
Apr 22, 2025
-
What Are The 4 Characteristics Of The State
Apr 22, 2025
Related Post
Thank you for visiting our website which covers about Aggregate Planning Is Capacity Planning For . We hope the information provided has been useful to you. Feel free to contact us if you have any questions or need further assistance. See you next time and don't miss to bookmark.