A Fan Is To Produce A Constant Airspeed Of 40
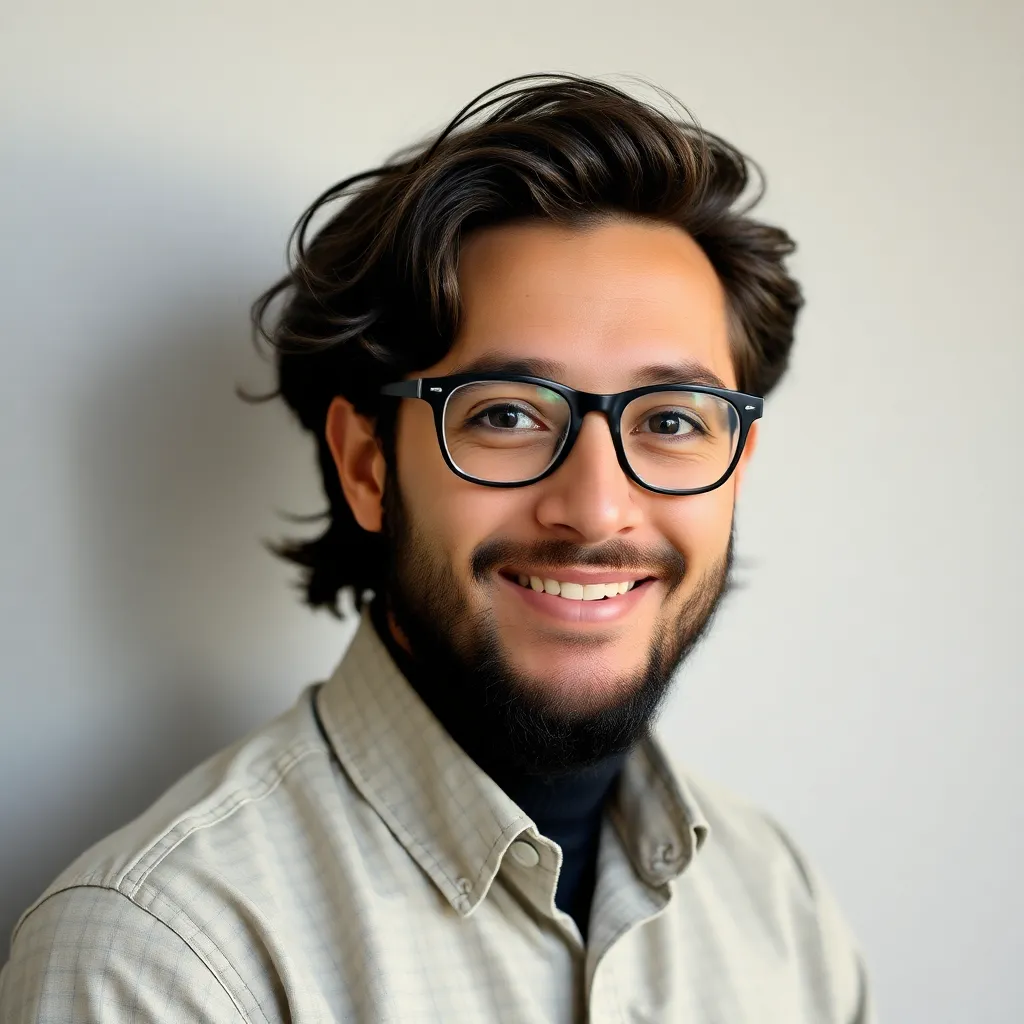
New Snow
Apr 26, 2025 · 6 min read

Table of Contents
Designing a Fan to Produce a Constant Airspeed of 40 m/s: A Comprehensive Guide
Achieving a constant airspeed of 40 m/s (approximately 89 mph) with a fan presents significant engineering challenges. This speed is far beyond what typical household or industrial fans are designed for, demanding a deep understanding of aerodynamics, motor selection, blade design, and control systems. This article delves into the intricate aspects of designing such a system, exploring the key considerations and potential solutions.
Understanding the Challenges: Why 40 m/s is Difficult
Producing a constant 40 m/s airspeed isn't simply a matter of choosing a powerful motor and large fan blades. Several factors complicate the design:
1. Aerodynamic Complexity:
At high speeds, air behaves differently. The airflow becomes turbulent, leading to inconsistencies in speed and pressure. Factors like blade profile, tip speed, and the overall fan geometry significantly impact the efficiency and consistency of airflow. Simple fan designs are ineffective at such high velocities, necessitating sophisticated blade profiles optimized for high-speed performance. This might involve advanced computational fluid dynamics (CFD) simulations to refine the blade design for optimal performance and minimal turbulence.
2. Motor Requirements:
Generating a consistent 40 m/s airspeed demands a substantial amount of power. The motor must be capable of delivering this power continuously without overheating or failing. Factors such as motor efficiency, torque characteristics at high speeds, and thermal management are critical. Specialized high-performance motors with robust cooling systems are likely necessary. The selection process would involve considering factors like power-to-weight ratio, efficiency curves, and operating temperature ranges.
3. Structural Integrity:
The fan blades and supporting structure must withstand the significant forces generated at 40 m/s. The centrifugal forces acting on the blades are immense, requiring robust materials and a carefully designed structure to prevent failure. Stress analysis, using finite element analysis (FEA) software, is crucial to ensure the integrity of the fan under these extreme operating conditions. Material selection becomes a critical aspect, prioritizing high strength-to-weight ratios and fatigue resistance.
4. Control Systems:
Maintaining a precisely constant airspeed requires a sophisticated control system. Fluctuations in power supply, changes in air density, or even minor variations in the fan's operational state can impact the airspeed. A feedback control loop, using sensors to measure the airspeed and adjust the motor speed accordingly, is indispensable. This necessitates the integration of accurate airspeed sensors (e.g., Pitot tube, hot-wire anemometer) and a control algorithm capable of maintaining the desired speed despite perturbations. The control system design needs to consider stability, responsiveness, and robustness.
5. Noise Reduction:
High-speed fans are inherently noisy. The turbulent airflow and high rotational speeds generate significant noise pollution. Strategies for noise reduction are vital, including aerodynamic optimization of blade design, acoustic treatment of the fan housing, and the use of noise-dampening materials. This aspect of the design requires collaboration with acoustics engineers.
Design Considerations: Key Components and Choices
Let's explore the critical components and design choices necessary to achieve a constant 40 m/s airspeed:
1. Fan Blade Design:
Blade Profile: High-speed fan blades require a carefully optimized profile to maximize efficiency and minimize turbulence. Advanced airfoil designs, often used in aircraft propellers, could be adapted for this purpose. The profile's shape, camber, and thickness distribution all contribute to the efficiency and stability of the airflow.
Number of Blades: The number of blades influences the airflow characteristics. A greater number of blades might lead to smoother airflow but could increase manufacturing complexity and weight. Computational fluid dynamics (CFD) simulations are crucial in determining the optimal number of blades for consistent high-speed performance.
Blade Material: Strong, lightweight materials are essential. High-strength composites, such as carbon fiber reinforced polymers (CFRP), are potential candidates for maximizing strength while minimizing weight and centrifugal forces.
2. Motor Selection:
Power Requirements: The power requirement is significant. Estimating this would involve calculations considering the airflow rate, air density, and the desired airspeed. Further optimization would come from aerodynamic analysis to reduce power losses.
Motor Type: High-efficiency AC or DC motors with high power-to-weight ratios are suitable candidates. The motor's torque curve at high speeds is particularly important to ensure consistent performance.
Cooling System: A robust cooling system is vital to prevent motor overheating at high power output. This could involve forced air cooling, liquid cooling, or a combination of both.
3. Structural Design:
Material Selection: The fan housing and supporting structure must withstand significant stresses. High-strength materials, such as aluminum alloys or composites, are necessary to ensure structural integrity.
Finite Element Analysis (FEA): FEA simulations are crucial to predict stress distributions under operational conditions and optimize the design for maximum strength and minimum weight.
Vibration Dampening: High-speed operation can generate vibrations that could lead to structural failure or noise problems. Vibration dampening measures, such as incorporating vibration isolators and designing the structure to minimize resonance frequencies, are essential.
4. Control System:
Airspeed Sensing: Precise airspeed measurement is critical. A Pitot tube or a hot-wire anemometer could provide accurate real-time feedback on the airspeed.
Control Algorithm: A closed-loop control algorithm (e.g., PID controller) is essential to maintain the desired airspeed. The algorithm should adjust the motor speed based on the measured airspeed, ensuring stability and responsiveness.
Safety Features: Over-speed protection, overload protection, and emergency shutdown mechanisms should be incorporated to ensure safe operation.
5. Noise Reduction Strategies:
Aerodynamic Optimization: Careful blade design and housing geometry can significantly reduce noise generation.
Acoustic Treatment: Acoustic materials can be integrated into the fan housing to absorb noise and reduce overall sound levels.
Vibration Isolation: Minimizing vibrations reduces noise transmission.
Testing and Iteration: Refining the Design
Creating this high-speed fan requires iterative testing and refinement. This involves:
- Computational Fluid Dynamics (CFD) Simulation: CFD simulations provide a virtual environment to test different blade designs and predict airflow characteristics before physical prototypes are built.
- Prototype Testing: Physical prototypes are necessary to validate simulations and identify any unforeseen problems.
- Performance Monitoring: Extensive testing is required to monitor performance parameters like airspeed consistency, power consumption, noise levels, and structural integrity under various operating conditions.
- Optimization: Based on test results, the design should be iteratively optimized to improve performance and address any issues identified.
Conclusion: A Multidisciplinary Engineering Challenge
Designing a fan to produce a constant 40 m/s airspeed is a demanding engineering undertaking. It requires a multidisciplinary approach, combining expertise in aerodynamics, mechanical engineering, electrical engineering, and control systems. Through careful consideration of blade design, motor selection, structural integrity, control systems, and noise reduction strategies, combined with rigorous testing and iterative refinement, this ambitious goal can be achieved. The application of advanced simulation tools like CFD and FEA is paramount in optimizing the design for both performance and safety. The challenge underscores the complexities of high-speed airflow and the need for sophisticated engineering solutions.
Latest Posts
Latest Posts
-
Why Is The Median Resistant But The Mean Is Not
Apr 26, 2025
-
Which Of The Following Is An Objective Finding
Apr 26, 2025
-
Aha Basic Life Support Exam C
Apr 26, 2025
-
What Is The Purpose Of The Lower Pyloric Sphincter
Apr 26, 2025
-
The Immune System Hhmi Biointeractive Answer Key
Apr 26, 2025
Related Post
Thank you for visiting our website which covers about A Fan Is To Produce A Constant Airspeed Of 40 . We hope the information provided has been useful to you. Feel free to contact us if you have any questions or need further assistance. See you next time and don't miss to bookmark.