A Company Studied The Number Of Lost-time Accidents
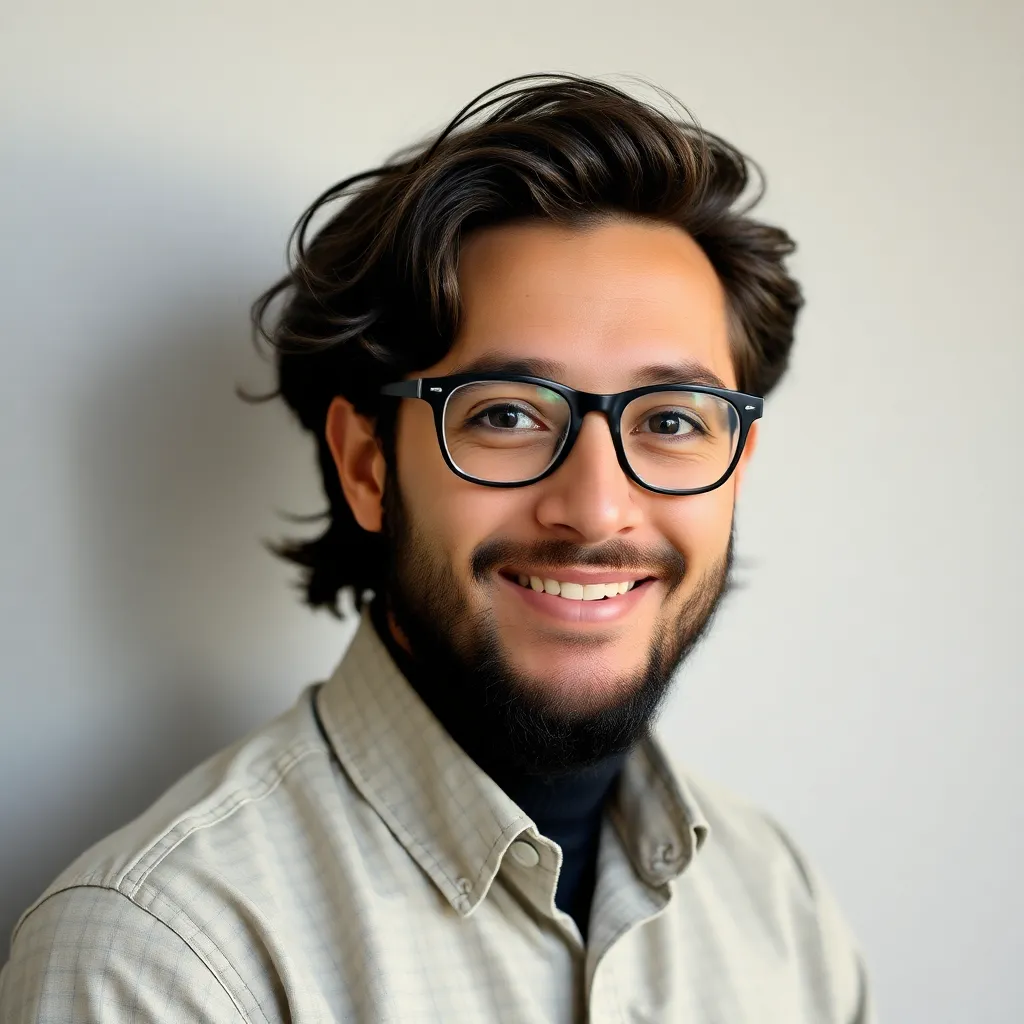
New Snow
Apr 24, 2025 · 6 min read

Table of Contents
A Company Studied the Number of Lost-Time Accidents: Unveiling Trends and Implementing Effective Safety Strategies
Lost-time accidents (LTAs) represent a significant concern for any company, impacting productivity, morale, and ultimately, the bottom line. A comprehensive study of LTA data allows organizations to identify trends, pinpoint contributing factors, and implement targeted safety strategies for a safer and more productive work environment. This in-depth article will explore a hypothetical company's analysis of its lost-time accidents, examining the methodology, findings, and resulting improvements in workplace safety.
Understanding the Data: Methodology and Collection
Our hypothetical company, "Innovative Industries," embarked on a rigorous study of its LTAs over a five-year period (2018-2022). The initial step involved defining what constitutes a lost-time accident. This included any injury or illness resulting in an employee missing one or more workdays. This crucial definition ensured consistency in data collection and analysis.
Data Sources and Collection Methods:
- Incident Reports: Innovative Industries utilizes a detailed incident reporting system, requiring employees to report all injuries, no matter how minor. These reports capture crucial information including date, time, location, nature of injury, contributing factors, and witness statements. This comprehensive approach minimizes underreporting, a common issue in LTA studies.
- Medical Records: Access to employee medical records (with appropriate privacy safeguards in place) provided further detail on the severity and nature of injuries, facilitating a more precise analysis.
- Safety Audits: Regular safety audits conducted by both internal and external safety professionals helped identify potential hazards and areas needing improvement before they resulted in accidents. These audits provided valuable context to the LTA data.
- Employee Surveys: Anonymous employee surveys were conducted to gather insights into perceived safety risks and suggestions for improvement. This qualitative data enriched the quantitative data from incident reports and audits.
Data Cleaning and Preparation:
Before analysis, the collected data underwent a thorough cleaning process. This involved checking for inconsistencies, correcting errors, and handling missing values. Data standardization ensured that all information was presented in a consistent format, facilitating accurate analysis.
Analyzing the Data: Trends and Patterns
After cleaning and preparing the data, Innovative Industries utilized various analytical techniques to identify trends and patterns in its LTA data.
Temporal Trends:
Analyzing the data over the five-year period revealed some interesting temporal trends. There was a noticeable spike in LTAs in 2020, which coincided with a significant increase in production output to meet a surge in demand. This highlighted the importance of managing workload and ensuring adequate staffing levels to maintain safety standards during peak periods.
Spatial Trends:
Analyzing the location of LTAs within the company's facilities revealed higher incident rates in certain areas, such as the manufacturing floor and warehouse. This spatial clustering pointed to potential environmental hazards or deficiencies in safety protocols in those specific locations.
Injury Type Analysis:
Innovative Industries categorized LTAs based on the type of injury sustained. The most common injuries were musculoskeletal disorders (MSDs), specifically back injuries and strains, accounting for approximately 40% of all LTAs. This highlighted the need for targeted ergonomics training and improvements in workplace ergonomics.
Root Cause Analysis:
A crucial aspect of the study involved root cause analysis for each LTA. This involved investigating the underlying factors that contributed to each incident. Common causes identified included inadequate training, unsafe working practices, poorly maintained equipment, and insufficient personal protective equipment (PPE).
Implementing Safety Strategies: Proactive Measures
The findings from Innovative Industries' LTA study provided valuable insights that led to the implementation of several proactive safety strategies.
Enhanced Training Programs:
Following the identification of inadequate training as a contributing factor to many LTAs, the company invested in enhanced training programs focusing on safe work practices, proper use of equipment, and hazard recognition. The training incorporated hands-on simulations and practical exercises to reinforce learning.
Ergonomic Improvements:
The high incidence of MSDs prompted a significant investment in ergonomic improvements. This involved redesigning workstations to improve posture and reduce strain, providing employees with adjustable chairs and desks, and introducing regular stretching breaks.
Equipment Maintenance and Upgrades:
The study highlighted the role of poorly maintained equipment in several LTAs. Innovative Industries implemented a rigorous equipment maintenance schedule, involving regular inspections, preventative maintenance, and timely repairs. Outdated equipment was progressively upgraded to safer, more modern alternatives.
Improved PPE Provision and Enforcement:
The study revealed inconsistent use of PPE. The company addressed this by improving PPE provision, ensuring adequate supply and proper fit for all employees. Stricter enforcement of PPE usage, including regular inspections and disciplinary measures for non-compliance, was also implemented.
Safety Culture Enhancement:
Beyond specific interventions, Innovative Industries focused on fostering a strong safety culture. This involved promoting open communication, encouraging employees to report hazards without fear of retribution, and rewarding safe work practices. Regular safety meetings and campaigns were conducted to reinforce safety awareness and promote proactive participation.
Measuring the Effectiveness of Safety Strategies: Continuous Improvement
The success of the implemented safety strategies was continuously monitored and evaluated. Key performance indicators (KPIs) were established, including the LTA rate, number of near misses reported, and employee satisfaction with safety measures. Regular reviews of these KPIs allowed for adjustments to the safety program, ensuring ongoing effectiveness.
Data-Driven Decision Making:
The data from the LTA study continued to be used for ongoing data-driven decision-making. Regular analysis of the KPIs helped identify areas needing further attention and allowed for timely adjustments to the safety program.
Feedback Mechanisms:
Multiple feedback mechanisms were implemented to ensure continuous improvement. These included regular safety meetings, anonymous surveys, and suggestion boxes, providing employees with platforms to voice their concerns and offer suggestions.
Conclusion: A Holistic Approach to Workplace Safety
Innovative Industries’ study of lost-time accidents exemplifies the importance of a data-driven approach to workplace safety. By meticulously collecting, analyzing, and interpreting LTA data, the company successfully identified contributing factors, implemented targeted safety strategies, and established mechanisms for continuous improvement. The success of this approach demonstrates that a holistic and proactive approach to workplace safety, incorporating training, ergonomic improvements, equipment maintenance, and a strong safety culture, is essential for creating a safer and more productive work environment. The long-term benefits of such an approach extend beyond reduced LTAs, encompassing improved employee morale, enhanced productivity, and a positive impact on the company's overall reputation. By prioritizing safety, Innovative Industries not only protects its workforce but also strengthens its competitive advantage.
This detailed analysis highlights the crucial role of data in driving effective safety initiatives. The ongoing monitoring and evaluation of safety strategies ensure continuous improvement and a commitment to maintaining a safe and productive workplace. The success of this hypothetical company demonstrates that a proactive, data-driven approach is vital for any organization aiming to minimize lost-time accidents and cultivate a strong safety culture. Furthermore, the investment in safety is not merely a cost but a strategic investment that yields significant long-term returns in terms of reduced costs associated with accidents, improved employee morale and productivity, and enhanced reputation. It underscores the importance of viewing safety not just as a compliance issue, but as a core value that underpins organizational success.
Latest Posts
Latest Posts
-
Horizontal Analysis Of Comparative Financial Statements Includes
Apr 24, 2025
-
The Distinguishing Characteristic In Win Lose Problem Solving Is
Apr 24, 2025
-
Faster Communication And Synchronization Are Two Advantages Of
Apr 24, 2025
-
Causes For Scope Creep Can Include
Apr 24, 2025
-
Chapter 15 Nutrition And Hydration Workbook Answers
Apr 24, 2025
Related Post
Thank you for visiting our website which covers about A Company Studied The Number Of Lost-time Accidents . We hope the information provided has been useful to you. Feel free to contact us if you have any questions or need further assistance. See you next time and don't miss to bookmark.